klayus
Newbie level 1

Hello, every one. I should introduce my self first
My name is Dragos, i'm 30 years old, and i'm from Romania. I'm an electronics engineer.
About 2 years ago I woke up at 6 (instead of 7) cause my girlfriends birthday was coming up and I wanted to make for her a small heart shaped circuit that lights up at night. She doesn’t like the dark and wanted a small night lamp. Well I’ve built the circuit with the classic toner transfer technique and it was a mess. I’ve never got good results with toner but this was one of those days that it didn’t want to work at all. And trying to cut a heart shape out of pcb by hand didnt turn out as good as i was imagining it. So out of frustration I’ve decided to build my own cnc machine, designed for rapid pcb etching, cutting, I love the silkscreen on top so I wanted that too, makes life so much easier when you’re assembling your circuit to see the components instead of having to go back and forth to the computer for details. I really hate loud repeating noises, hate having to deal with chemicals and never found good enough paper for toner transfer. And if all this wasn’t enough motivation I especially hate drilling holes in pcbs. It’s a major pain, I hate that dust, that smell and it takes a lot of time, and it breaks a lot of drill bits. Clumsy me.
So pCarve 1.0 took birth. It was made from 10 mm thick transparent acrylic, it was kinda sloppy but it did the job. I just had to run the gcode and watch it “dance” and finish my pcb. Few things in life I enjoy more than watching my machine carving my circuit.
I wasn’t really satisfied, I knew I could improve it. So pCarve 2.0 took birth. It’s made from polyamide, it has an work area of 285 x 200 x 40 mm height. It’s fast, accurate and best of all it’s silent. At least compared to the rest of the cncs I’ve seen or worked with.
I’m using t2.5 belt with steel insertion for the X and Y axes, trapeze screw for the Z. it has an er11 collet chuck, it runs in 12 mm linear rails. The machine is controlled by grbl on an arudino nano. It has drv8825 drivers, the motor is a brushless motor that spins a precision ground shank. The start stop and speed of the motor is controlled by grbl as well.
Here are some picture with the machine:
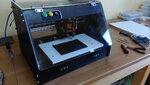
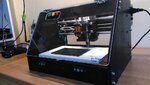
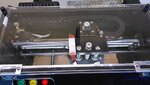
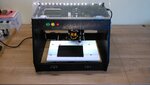
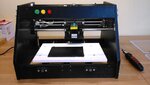
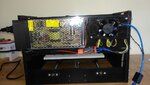
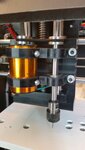
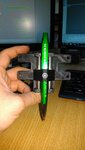
Here is a small solder station enclosure I’ve made with the machine:
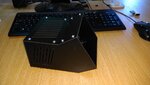
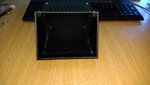
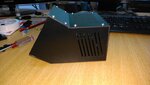
Here are some videos with it:
https://youtu.be/7FrBSVhmA8w
https://youtu.be/sviWAfxiDu4
https://youtu.be/TJDm6ogdWXw
https://youtu.be/OmcZ4SYHqT8
https://youtu.be/vZdb3EsL39U
https://youtu.be/tJZHVOiri-c
https://youtu.be/W1e188_DKwo
Here are some more pics with the laser engraver and stuff i've made with it:
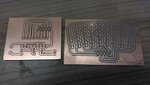
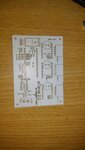
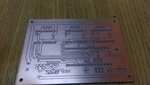
here is a double-sided board. just the pad isolation on the other side.
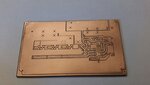
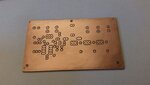
something with small pads
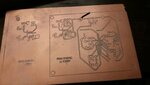
it can also hold a laser engraver, and also has a pen holder. I’m planning on adding a 3d printer extruder, but I’m not sure yet because of the small working height.
Don’t know what else to say about it here.
If you guys have any questions, ask
Best regards
Dragos
About 2 years ago I woke up at 6 (instead of 7) cause my girlfriends birthday was coming up and I wanted to make for her a small heart shaped circuit that lights up at night. She doesn’t like the dark and wanted a small night lamp. Well I’ve built the circuit with the classic toner transfer technique and it was a mess. I’ve never got good results with toner but this was one of those days that it didn’t want to work at all. And trying to cut a heart shape out of pcb by hand didnt turn out as good as i was imagining it. So out of frustration I’ve decided to build my own cnc machine, designed for rapid pcb etching, cutting, I love the silkscreen on top so I wanted that too, makes life so much easier when you’re assembling your circuit to see the components instead of having to go back and forth to the computer for details. I really hate loud repeating noises, hate having to deal with chemicals and never found good enough paper for toner transfer. And if all this wasn’t enough motivation I especially hate drilling holes in pcbs. It’s a major pain, I hate that dust, that smell and it takes a lot of time, and it breaks a lot of drill bits. Clumsy me.
So pCarve 1.0 took birth. It was made from 10 mm thick transparent acrylic, it was kinda sloppy but it did the job. I just had to run the gcode and watch it “dance” and finish my pcb. Few things in life I enjoy more than watching my machine carving my circuit.
I wasn’t really satisfied, I knew I could improve it. So pCarve 2.0 took birth. It’s made from polyamide, it has an work area of 285 x 200 x 40 mm height. It’s fast, accurate and best of all it’s silent. At least compared to the rest of the cncs I’ve seen or worked with.
I’m using t2.5 belt with steel insertion for the X and Y axes, trapeze screw for the Z. it has an er11 collet chuck, it runs in 12 mm linear rails. The machine is controlled by grbl on an arudino nano. It has drv8825 drivers, the motor is a brushless motor that spins a precision ground shank. The start stop and speed of the motor is controlled by grbl as well.
Here are some picture with the machine:
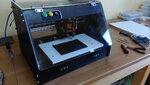
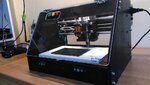
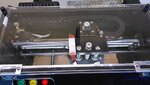
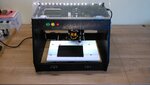
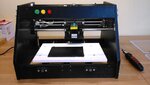
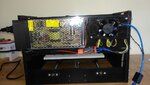
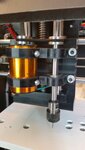
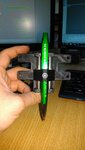
Here is a small solder station enclosure I’ve made with the machine:
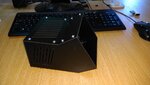
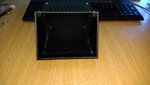
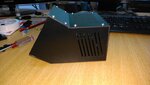
Here are some videos with it:
https://youtu.be/7FrBSVhmA8w
https://youtu.be/sviWAfxiDu4
https://youtu.be/TJDm6ogdWXw
https://youtu.be/OmcZ4SYHqT8
https://youtu.be/vZdb3EsL39U
https://youtu.be/tJZHVOiri-c
https://youtu.be/W1e188_DKwo
Here are some more pics with the laser engraver and stuff i've made with it:
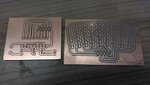
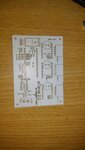
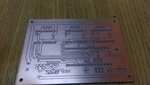
here is a double-sided board. just the pad isolation on the other side.
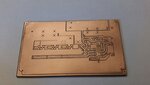
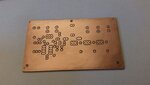
something with small pads
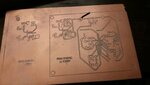
it can also hold a laser engraver, and also has a pen holder. I’m planning on adding a 3d printer extruder, but I’m not sure yet because of the small working height.
Don’t know what else to say about it here.
If you guys have any questions, ask
Best regards
Dragos