OrdosDeviator
Member level 1

Starting point:
Power +5V (now it is taken from +24V by MC34063A output ripple 40-400mVpp).
8 Pt100 RTD channels, required range 0C - 300C.
Desirable measure accuracy is not less 1C. (0.5C or 0.1C would be awesome also
)
Objective: to build up to 8 temperature measure channels based on PIC18F46K22.
I have built Pt100 channel as you can see at the picture.
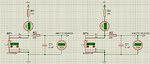
Proteus simulation tells me the biggest voltage span is reached with R1=~150 Ohm.
For temperature range 0-300C the voltages are from 2V to 3V so the span is about 1V.
Real implementation gave me 2.1V for 20C so I consider Proteus quit trustworthy.
PIC18 ADC VREF+ was connected to power.
I collided with the situation ADC gaves me ripple up to 4 bits wich is unacceptable.
Also 1024 bits ADC gives resolution 204 bits/1V, in my case it would be 204bit/300C
so I cant reach accuracy 1C.
PIC18F46K22 has stable VOLTAGE REFERENCE setable 1.024/2.048/4.096V and I can switch it to out pin,
bit it can't supply 8 Pt100 cahnnels. Now every channel eats ~20mA.
So, I need advice in which direction should I dig.
- May be/how to get stable 500-1000mA 5V power (from 24V) stable enough to feed temperature sensors and all my scheme.
- May be/how to get independent stable power for Pt100 feeding.
- How to expand voltage range for Pt100 0-300C to reach ADC accuracy about 1bit/1C.
Restrictables:
Pt100 cant be changed.
Additional individual chip for every pt100 is unacceptable (but common chip for all channels is acceptable).
Part replacement cant be very expensive.
Power +5V (now it is taken from +24V by MC34063A output ripple 40-400mVpp).
8 Pt100 RTD channels, required range 0C - 300C.
Desirable measure accuracy is not less 1C. (0.5C or 0.1C would be awesome also
Objective: to build up to 8 temperature measure channels based on PIC18F46K22.
I have built Pt100 channel as you can see at the picture.
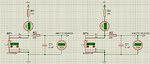
Proteus simulation tells me the biggest voltage span is reached with R1=~150 Ohm.
For temperature range 0-300C the voltages are from 2V to 3V so the span is about 1V.
Real implementation gave me 2.1V for 20C so I consider Proteus quit trustworthy.
PIC18 ADC VREF+ was connected to power.
I collided with the situation ADC gaves me ripple up to 4 bits wich is unacceptable.
Also 1024 bits ADC gives resolution 204 bits/1V, in my case it would be 204bit/300C
so I cant reach accuracy 1C.
PIC18F46K22 has stable VOLTAGE REFERENCE setable 1.024/2.048/4.096V and I can switch it to out pin,
bit it can't supply 8 Pt100 cahnnels. Now every channel eats ~20mA.
So, I need advice in which direction should I dig.
- May be/how to get stable 500-1000mA 5V power (from 24V) stable enough to feed temperature sensors and all my scheme.
- May be/how to get independent stable power for Pt100 feeding.
- How to expand voltage range for Pt100 0-300C to reach ADC accuracy about 1bit/1C.
Restrictables:
Pt100 cant be changed.
Additional individual chip for every pt100 is unacceptable (but common chip for all channels is acceptable).
Part replacement cant be very expensive.