--BawA--
Advanced Member level 1

- Joined
- Nov 28, 2012
- Messages
- 479
- Helped
- 43
- Reputation
- 86
- Reaction score
- 42
- Trophy points
- 1,318
- Location
- Noida, INDIA
- Activity points
- 4,931
today i have tested my hbridge circuit again with low voltage (20v) and in output as i connected a resistive load ,i got the sine wave in oscciloscope.i am attaching the image below
https://obrazki.elektroda.pl/3578304900_1372178877.jpg
https://obrazki.elektroda.pl/6054555100_1372178880.jpg
i have tested my hbridge circuit with max dc bus voltage of 32v,
- - - Updated - - -
hii ,
i have also seen my 311 v dc bus voltage on DSO, and it was like
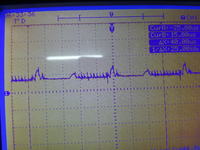
how to get pure dc , i have used an lc filter in output of the bridge rectifier , 3mh inductor and 47uf electrolytic capacitor,also i have added two 0.1uf ceramic capacitor in parallel to electrolytic capacitor,,, but there is ripple in output,,how to get a clean dc bus??
- - - Updated - - -
i dont have a dc source of 110v , i have dc source of 311v that my circuit is producing, tomorrow, i will check my hbridge with 311v dc, should i proceed with that? because ahsan is saying that ir2110 is not good for 311vdc bus,? what should i do now??
- - - Updated - - -
IN my design the high side mosfet of one arm hbridge is kept ON for 10ms,while in the same time ,the low side mosfet of other arm is getting a spwm signal.
and after adding a resisitive load i got the sine wave,.
but should i test my circuit with 311v dc ?,, coz i have made my circuit 6 times,,and before filter ,it works gud,but as i connect the filter ,my mosfets blown out ,, earlier i was using torroidal core for inductor design ,but this time i am using ETD39 core with 1mm gap for my inductor as suggested by FvM,, i have made it to 5mh , and also used 0.22uf capacitor
this is my circuit
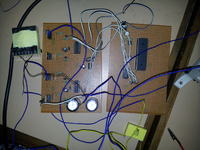
so should i do high voltage test of my hbridge now? or make some changes?
https://obrazki.elektroda.pl/3578304900_1372178877.jpg
https://obrazki.elektroda.pl/6054555100_1372178880.jpg
i have tested my hbridge circuit with max dc bus voltage of 32v,
- - - Updated - - -
hii ,
i have also seen my 311 v dc bus voltage on DSO, and it was like
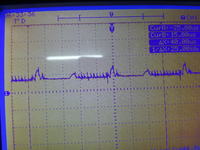
how to get pure dc , i have used an lc filter in output of the bridge rectifier , 3mh inductor and 47uf electrolytic capacitor,also i have added two 0.1uf ceramic capacitor in parallel to electrolytic capacitor,,, but there is ripple in output,,how to get a clean dc bus??
- - - Updated - - -
i dont have a dc source of 110v , i have dc source of 311v that my circuit is producing, tomorrow, i will check my hbridge with 311v dc, should i proceed with that? because ahsan is saying that ir2110 is not good for 311vdc bus,? what should i do now??
- - - Updated - - -
ahsan_i_h said:In these pdfs one of the arms of H bridge is driven by 50Hz and other arm is driven by PWM signal.
But, perhaps, In your design top mosfets of the arms are getting 50Hz signal and bottom mosfets of the arms getting PWM
signal (but 10ms alternately). Is that right ?
If it is right, then your filter requires a minimum load current to work as expected.
IN my design the high side mosfet of one arm hbridge is kept ON for 10ms,while in the same time ,the low side mosfet of other arm is getting a spwm signal.
and after adding a resisitive load i got the sine wave,.
but should i test my circuit with 311v dc ?,, coz i have made my circuit 6 times,,and before filter ,it works gud,but as i connect the filter ,my mosfets blown out ,, earlier i was using torroidal core for inductor design ,but this time i am using ETD39 core with 1mm gap for my inductor as suggested by FvM,, i have made it to 5mh , and also used 0.22uf capacitor
this is my circuit
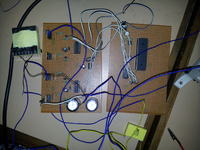
so should i do high voltage test of my hbridge now? or make some changes?