pgib8
Member level 2

Hi Everyone. I'm pretty new to RF and I'm trying to match a PCB trace antenna to 50 ohms.
As I change the matching components and read the impedance, the readings I get are very different from what I would have expected.
I'm measuring at 905MHz and the impedance seems to be moving sideways. If anybody has any pointers I sure would like to hear them.
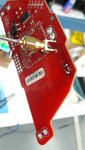
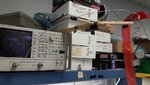
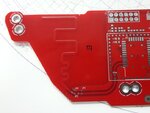

J1, closest to source, parallel component
J2, middle, series component
J3, closest to antenna, parallel component
point 1: starting without matching, using 0-ohm jumper at J2.
point 2: added 4.7pF at J3 (parallel)
point 3: decreased from 4.7 to 1pF
point 4: increased from 1 to 3.3pF
observing impedance moving sideways instead of down.
point 5: added 2.2nH at J2 (series)
point 6: increased 2.2 to 3.6nH
point 7: increased 3.6 to 6.2nH
observing further sideways movement
point 8: added 12nH at J1 (parallel)
point 9: increased from 12 to 22nH
point 10: replace J2 6.2nH with 0-ohm jumper (series).
As I change the matching components and read the impedance, the readings I get are very different from what I would have expected.
I'm measuring at 905MHz and the impedance seems to be moving sideways. If anybody has any pointers I sure would like to hear them.
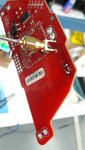
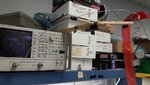
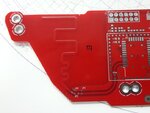

J1, closest to source, parallel component
J2, middle, series component
J3, closest to antenna, parallel component
point 1: starting without matching, using 0-ohm jumper at J2.
point 2: added 4.7pF at J3 (parallel)
point 3: decreased from 4.7 to 1pF
point 4: increased from 1 to 3.3pF
observing impedance moving sideways instead of down.
point 5: added 2.2nH at J2 (series)
point 6: increased 2.2 to 3.6nH
point 7: increased 3.6 to 6.2nH
observing further sideways movement
point 8: added 12nH at J1 (parallel)
point 9: increased from 12 to 22nH
point 10: replace J2 6.2nH with 0-ohm jumper (series).