eagle1109
Full Member level 6

- Joined
- Nov 20, 2014
- Messages
- 393
- Helped
- 4
- Reputation
- 10
- Reaction score
- 7
- Trophy points
- 1,298
- Location
- Saudi Arabia
- Activity points
- 5,956
Hello,
I work in microcontrollers course in diploma college and I've been training this course for like 2 years now.
I faced different problems with our dev boards because they are basic for voltage input there's only a diode, maybe it's a Zener but I don't think it provides much protection for the components because we already lost several PICkits + PIC16F877As.
I don't want to still loosing PICkits so often. I want to modify the dev board with anything that provides upto like 5.5V max.
I think there are different ways to do it:
1. use lm7805
2. search for dedicated OVP chips, I did a quick search and found one that could be interesting to me which is this one:
I think it's easy to include in the board with some modifications. external connections would be ok as long as we protect our stuff from trainees missing adjusting the variable power supply.
I thought of other solutions, which is to buy a constant 5V adapter, I have one that is 5V/2A, but actually that PICkit didn't catch the 5V ! I don't know why it had to be supplied from the bench variable PSU.
This is our dev board and I'm sketching the power input area with yellow circle.
I work in microcontrollers course in diploma college and I've been training this course for like 2 years now.
I faced different problems with our dev boards because they are basic for voltage input there's only a diode, maybe it's a Zener but I don't think it provides much protection for the components because we already lost several PICkits + PIC16F877As.
I don't want to still loosing PICkits so often. I want to modify the dev board with anything that provides upto like 5.5V max.
I think there are different ways to do it:
1. use lm7805
2. search for dedicated OVP chips, I did a quick search and found one that could be interesting to me which is this one:
LTC4360-1 LTC4360-2 Datasheet and Product Info | Analog Devices
The LTC4360 overvoltage protection controller safeguards 2.5V to 5.5V systems from power supply overvoltage. It is designed for portable devices with multiple power supply options including wall adaptors, car battery adaptors and USB ports. The LTC4360 controls an external N-channel MOSFET in...www.analog.com
I think it's easy to include in the board with some modifications. external connections would be ok as long as we protect our stuff from trainees missing adjusting the variable power supply.
I thought of other solutions, which is to buy a constant 5V adapter, I have one that is 5V/2A, but actually that PICkit didn't catch the 5V ! I don't know why it had to be supplied from the bench variable PSU.
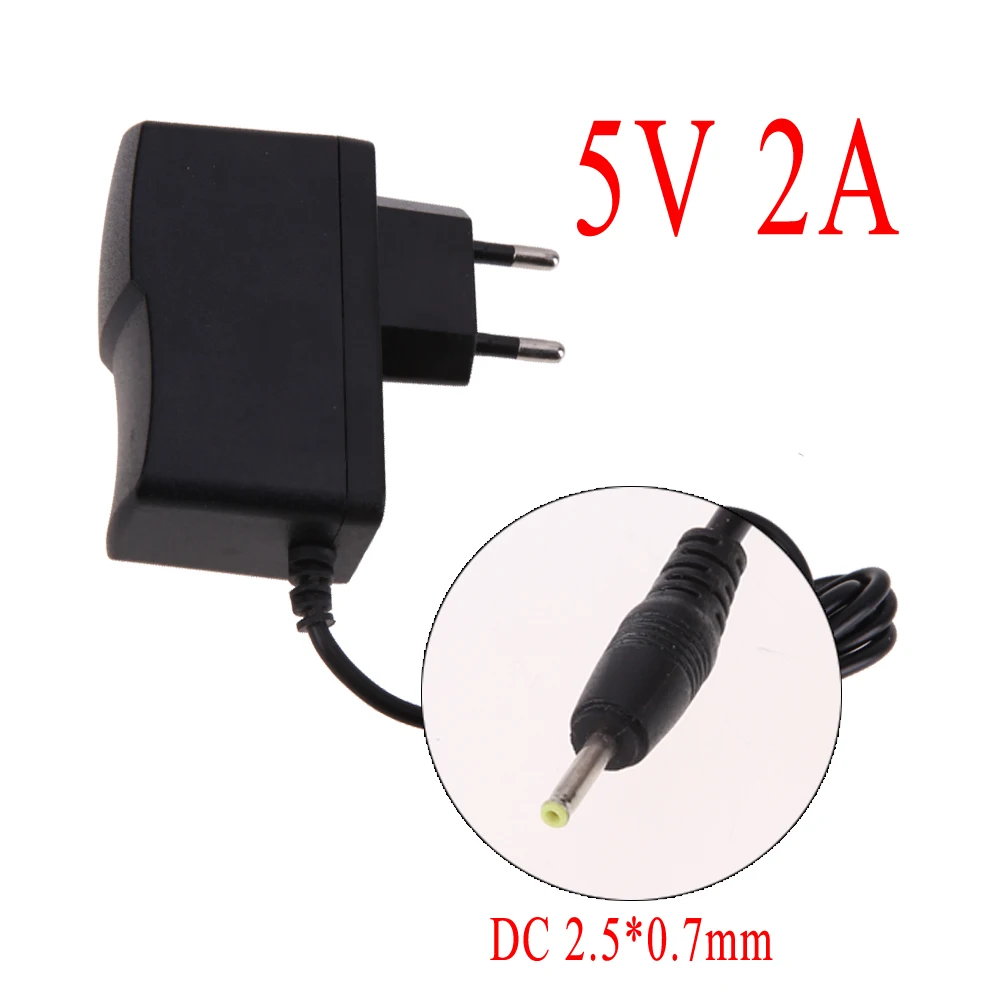
This is our dev board and I'm sketching the power input area with yellow circle.
