abomin3v3l
Junior Member level 1

Hi.
I'm doing a RF remote control project using a PCB with microcontroller and with simple onboard antenna layout as transmitter and a 433.92MHz receiver RWS-371F-6 model. Here is the datasheet of the receiver: https://www.es.co.th/Schemetic/PDF/RWS-371F-6.PDF
I don't have knowledge about RF design, just electronics and MCU programming. I'm using manchester encoding/decoding @ 1000bps to improve the communication distance from receptor board to the transmitter. 'RF-TX' is a 0V~5V signal.
The circuit of RF was copied from a board of a garage door opener, but I included my own microcontroller to the PCB schematic and I have some prototypes of the board. The values of resistors (150 Ohms, 47K, 47 Ohms) was also copied from the garage opener transmitter board. Here I am showing the layout of my board and the values/part number of the components. I've mounted a few pF capacitor combination values (0805) for C2/C3. I have a capacitor sample book with many values on pF range, many values from 1 to 22pF. The communication TX/RX is working correctly, but I want to check if I can increase the distance range by using adequate values for C2/C3. Currently I'm using both as 1pF.
At the receptor, I'm using coil loaded antenna with 1/4 of wavelength, the same of the picture, tomorrow I will try a straight rigid wire of 1/2 of wavelength.
Well, as said, my doubt is around the correct values of C2/C3, can somebody who understand of RF desing calculate them easily? Or does this generate a kind of service that I have to contract a RF designer to calculate them to me?
Regards.
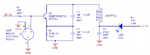
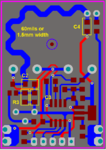
I'm doing a RF remote control project using a PCB with microcontroller and with simple onboard antenna layout as transmitter and a 433.92MHz receiver RWS-371F-6 model. Here is the datasheet of the receiver: https://www.es.co.th/Schemetic/PDF/RWS-371F-6.PDF
I don't have knowledge about RF design, just electronics and MCU programming. I'm using manchester encoding/decoding @ 1000bps to improve the communication distance from receptor board to the transmitter. 'RF-TX' is a 0V~5V signal.
The circuit of RF was copied from a board of a garage door opener, but I included my own microcontroller to the PCB schematic and I have some prototypes of the board. The values of resistors (150 Ohms, 47K, 47 Ohms) was also copied from the garage opener transmitter board. Here I am showing the layout of my board and the values/part number of the components. I've mounted a few pF capacitor combination values (0805) for C2/C3. I have a capacitor sample book with many values on pF range, many values from 1 to 22pF. The communication TX/RX is working correctly, but I want to check if I can increase the distance range by using adequate values for C2/C3. Currently I'm using both as 1pF.
At the receptor, I'm using coil loaded antenna with 1/4 of wavelength, the same of the picture, tomorrow I will try a straight rigid wire of 1/2 of wavelength.
Well, as said, my doubt is around the correct values of C2/C3, can somebody who understand of RF desing calculate them easily? Or does this generate a kind of service that I have to contract a RF designer to calculate them to me?
Regards.
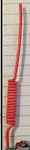
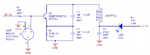
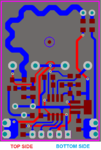
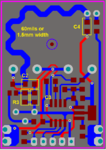