jojoe
Member level 1

Hi,
Yeah the size of the item is the only concern, apparently its 105mm x 61mm before it's fitted into a box.
I've found more info, Everyday Practical Electronics done a construction project with exactly the same item back in September 2008, I managed to find the article & have it as a pdf, there is a parts list & all the operating & construction details etc, You can download the PCB print & PIC hex from the EPE website.
I'm wondering if it would be possible to shrink the size of the unit down a bit as there looks to be a lot of spare space on the PCB.
Cheers.
Yeah the size of the item is the only concern, apparently its 105mm x 61mm before it's fitted into a box.
I've found more info, Everyday Practical Electronics done a construction project with exactly the same item back in September 2008, I managed to find the article & have it as a pdf, there is a parts list & all the operating & construction details etc, You can download the PCB print & PIC hex from the EPE website.
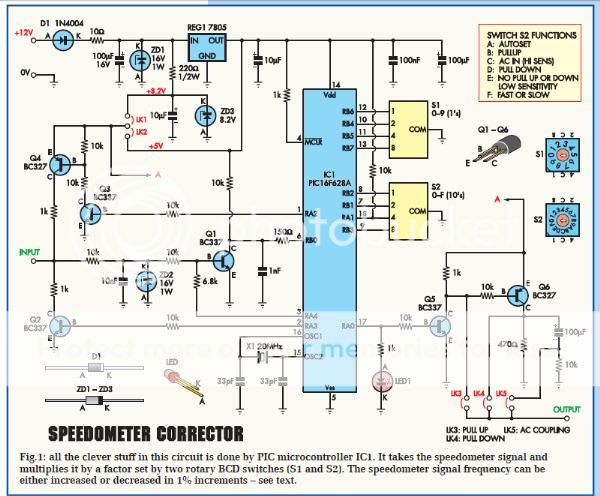
I'm wondering if it would be possible to shrink the size of the unit down a bit as there looks to be a lot of spare space on the PCB.
Cheers.