electrophile
Member level 2

I'm designing a 12VDC, 10A SMPS that would drive a brushless motor using the TL494. The motor has an inrush current of about 8A and a nominal current draw of around 5.5A. I was looking at TI's design guide here. The design example (page 24) they've done uses a 5V output (mine however would be 12V). I have two primary questions,
First: To get a 12V output, I'm guessing I would only need to change R8 and R9 divider to get the appropriate value at the error amplifier. Can I use the Vref (instead of dividing it) as one of the references for the error amplifier and then divide the 12V to 5V as the other reference for the error amplifier.
Second: The power switch seems to be a pair of NPN=PNP transistors. Can anyone recommend alternate parts for these? The NTE153 and NTE331 are not available in my part of the world. Also, can I replace this with say a power MOSFET? If so, what modifications would need to be done to power switch circuit?
Any advice would be much appreciated. Thanks!
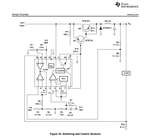
First: To get a 12V output, I'm guessing I would only need to change R8 and R9 divider to get the appropriate value at the error amplifier. Can I use the Vref (instead of dividing it) as one of the references for the error amplifier and then divide the 12V to 5V as the other reference for the error amplifier.
Second: The power switch seems to be a pair of NPN=PNP transistors. Can anyone recommend alternate parts for these? The NTE153 and NTE331 are not available in my part of the world. Also, can I replace this with say a power MOSFET? If so, what modifications would need to be done to power switch circuit?
Any advice would be much appreciated. Thanks!
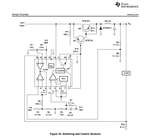