Roger Freeman
Junior Member level 2

Hello
For RF designs I have always specified a "solid" copper flood for ground and power planes, with sparing use of thermal reliefs if necessary (and avoided them for RF!).
However, I note that a lot of consumer/professional PCBs have planes like this:
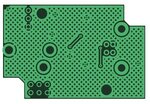
**broken link removed**
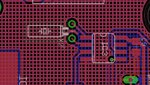
https://rayshobby.net/wordpress/wp-content/uploads/2013/05/pcbtrace20_new.jpg
whereby the copper fill is divided up into a grid rather outcome than being solid. I don't know why this is done - for a start off, it presumably takes longer to manufacture because it requires more etching, and it uses up more of the etchtant and prolongs the board's exposure to the etch process (with resultant undercutting of tracks being the likely risk).
So what's the advantage of using these "cross-hatched" or "gridded" or "checkerboard" floods? Is there a proper name for it?
RF
For RF designs I have always specified a "solid" copper flood for ground and power planes, with sparing use of thermal reliefs if necessary (and avoided them for RF!).
However, I note that a lot of consumer/professional PCBs have planes like this:
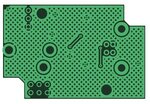
**broken link removed**
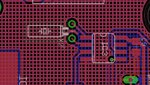
https://rayshobby.net/wordpress/wp-content/uploads/2013/05/pcbtrace20_new.jpg
whereby the copper fill is divided up into a grid rather outcome than being solid. I don't know why this is done - for a start off, it presumably takes longer to manufacture because it requires more etching, and it uses up more of the etchtant and prolongs the board's exposure to the etch process (with resultant undercutting of tracks being the likely risk).
So what's the advantage of using these "cross-hatched" or "gridded" or "checkerboard" floods? Is there a proper name for it?
RF
Last edited by a moderator: