Auric_
Junior Member level 2

Hello everyone.
If you look at the input circuit of almost every programmable controller that works with 24V discrete signals, you will see the following circuit (or functionally similar):
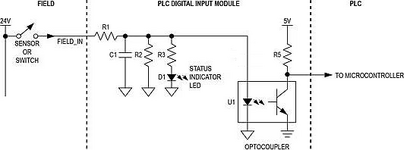
I want to understand, what functions are imposed on the voltage divider on R1 and R2 (don't pay attention to R3-D1 circuit, it may not exist, just as its installation may be before R1).
The actuation voltage can be achieved by selecting R1 and R5, and the device input current is rarely required to be greater than the resulting optocoupler LED current.
If you read, for example, this document, you can understand that resistor R2 is involved in setting the input current of the device, I have not yet realized another function and I will be very glad to receive an explanation regarding the presence of R2 in the circuit, as well as some technique that can give calculation of these parameters (resistances) of the circuit.
PS: Well, R2 can also dampen differential nanosecond interference, but C1 can also cope with this.
If you look at the input circuit of almost every programmable controller that works with 24V discrete signals, you will see the following circuit (or functionally similar):
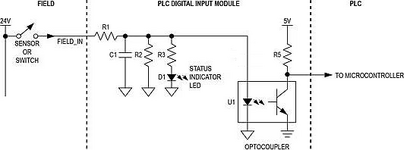
I want to understand, what functions are imposed on the voltage divider on R1 and R2 (don't pay attention to R3-D1 circuit, it may not exist, just as its installation may be before R1).
The actuation voltage can be achieved by selecting R1 and R5, and the device input current is rarely required to be greater than the resulting optocoupler LED current.
If you read, for example, this document, you can understand that resistor R2 is involved in setting the input current of the device, I have not yet realized another function and I will be very glad to receive an explanation regarding the presence of R2 in the circuit, as well as some technique that can give calculation of these parameters (resistances) of the circuit.
PS: Well, R2 can also dampen differential nanosecond interference, but C1 can also cope with this.