tanky321
Member level 1

scr circuit welder
I came across a circuit online to vary the 220V input into a welder. This is done to control the amount of current entering the piece being welded, using a foot pedal. The circuit has worked for many people.
I built the circuit, but it doesnt work. R2 blew when I would crank the pot up, and there was no current entering the welder. I dont know if the SCR fired or not, but it wouldnt weld or make a spark what so ever.
My initial thoughts are that the circuit was designed for a particular type of SCR, and mine isnt compatible.
Also, im an EE student but im just starting out, I have some circuit theory under my belt, but im not sure on how to tackle this problem.
Can anyone help me out?
Sorry for the size of the pictures, but I wanted to keep the detail.
Thank you!
I came across a circuit online to vary the 220V input into a welder. This is done to control the amount of current entering the piece being welded, using a foot pedal. The circuit has worked for many people.
I built the circuit, but it doesnt work. R2 blew when I would crank the pot up, and there was no current entering the welder. I dont know if the SCR fired or not, but it wouldnt weld or make a spark what so ever.
My initial thoughts are that the circuit was designed for a particular type of SCR, and mine isnt compatible.
Also, im an EE student but im just starting out, I have some circuit theory under my belt, but im not sure on how to tackle this problem.
Can anyone help me out?
Sorry for the size of the pictures, but I wanted to keep the detail.
Thank you!
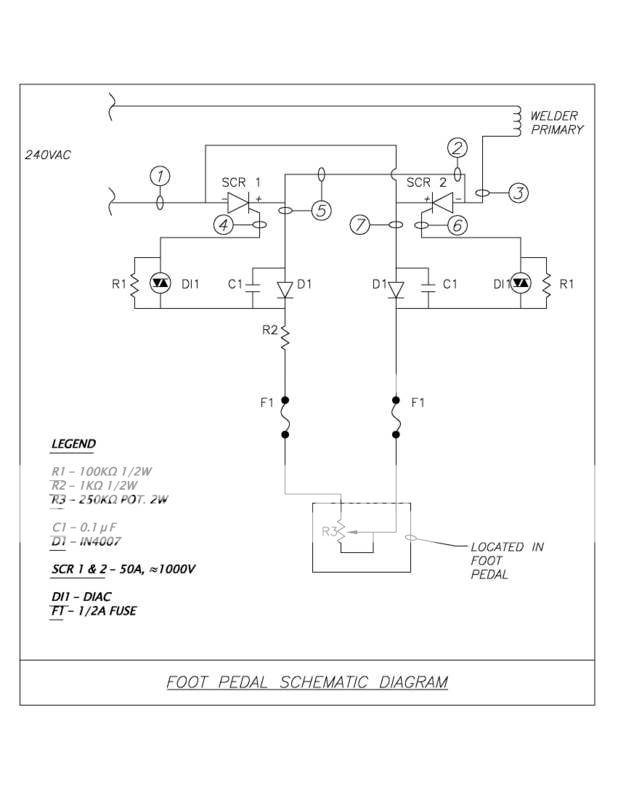
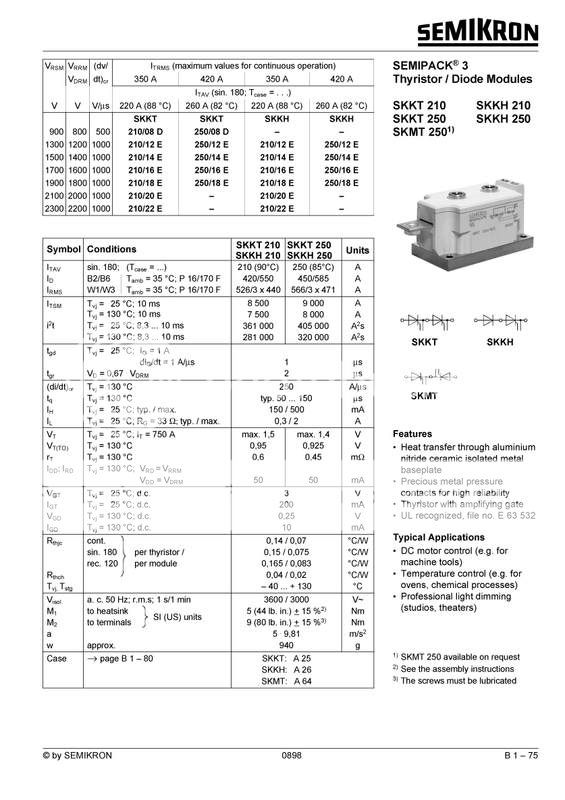

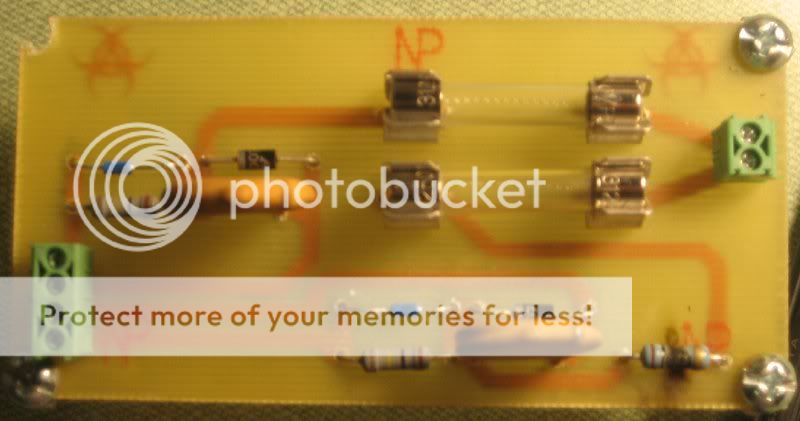