Vermes
Advanced Member level 4

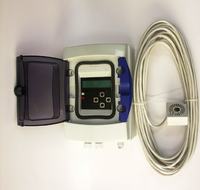
The driver is based on processor Atmega16/32, that controls optotriacs/triacs, measurement is made by the sensor SHT11. In assumptions, the driver was to have few additional functions such as communication with computer via RS232/RS458, protection against the attempt to start with open housing (eg. by the limit switch), measurement of the temperature inside the housing and emergency turning off the control when the temperature is too high.
The PCB was made by thermal transfer method using laser printer processed for ironing boards with prints (something similar to a device for lamination). The whole was cut and drilled on CNC milling machine, protected with lacquer for electronics. The board consists of two parts: control (display and buttons) and executive (processor, triacs, sockets). Inscriptions on the PCB were made by thermal transfer method. Housing IP65. Sensor SHT11 (with SF1 filter) was plugged on a screen twisted pair FTP 12m long. Software was written in C (WinAVR). Control is very simple, two-states with programmed minimum hysteresis for temperature and humidity. The driver was to switch on two contactors, which switch on the circuit triggering heating or humidifying rooms.
The current state is indicated by two diodes: blue – humidifying, red – heating. Other additional information are given on the display.
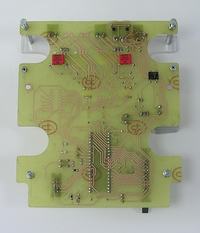
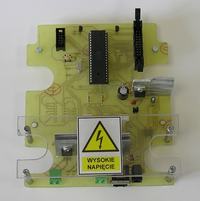
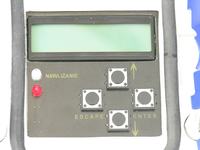
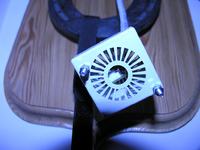
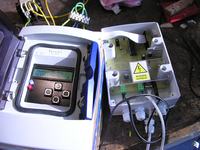
Link to original thread (useful attachment) – Sterownik temperatury i wilgotności, Atmega, SHT11