gzdeozc
Junior Member level 1

Hi,
I am new at microwave coupler design. I have designed a stripline directional coupler using Momentum assuming that the upper and lower ground are perfect cover, it worked well on simulation environment. But when I implemented it, I put pads on top ground in order to measure S21, S31, etc.. So I used a transition from stripline to microstrip. But as you guess, it didn't work. The directivity is very bad, the loss is bad. I guess there is a problem with my transition. I put here gerber films and need your valuable comments.
Thank you in advance..
Coupler:
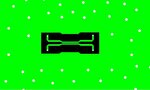
Top ground:
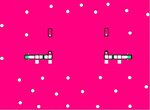
I am new at microwave coupler design. I have designed a stripline directional coupler using Momentum assuming that the upper and lower ground are perfect cover, it worked well on simulation environment. But when I implemented it, I put pads on top ground in order to measure S21, S31, etc.. So I used a transition from stripline to microstrip. But as you guess, it didn't work. The directivity is very bad, the loss is bad. I guess there is a problem with my transition. I put here gerber films and need your valuable comments.
Thank you in advance..
Coupler:
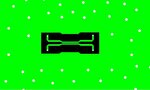
Top ground:
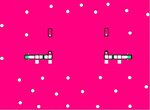