harvie
Full Member level 1

How to wire Strain Gauges without canceling each other?
Hi,
i am experimenting with various CNC touch probe designs and i've came across following setup using straingauges CA-glued to elastic frame holding the probe tip. I will probably use aluminum or acrylic as base for the strain gauge.
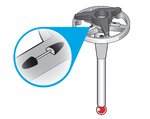
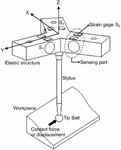
I wonder if there is a way to wire this using single instrumentation amplifier channel. (i am going to use HX711 inamp with integrated ADC).
Problem is that i am afraid that under certain angles of side load, the strain gauges can cancel each other when placed in single wheatstone bridge. Unlike personal scale (which has all strain gauges loaded in the same direction by person standing on top of it) these touch probe strain gauges will be loaded in both compression and tension randomly based on direction of touch. If this happens, the CNC will continue moving towards the probed object and break the probe. I need this to be as sensitive as possible without being affected by stepper motor vibrations and intertia of probe tips.
I don't really need to use the 3 beamed star topology showed in image. I can use any other strain gauge placement as long as it's at least kind of symetric. But i want to produce strain gauge based needle that will be sensitive to mechanical touch from any direction (both axial and radial). I can even use some kind of multiaxial strain gauge. But i am bit lost in the choices. Also they are usualy much more expensive...
I need this to work with sharp tip to have enough resolution. But i don't want to puncture the scanned object. I've tried with cheap chinese weighing scale. It's based on load cell and sensitive enough to react when i press my finger against the tip of the needle needle without puncturing my skin. So i think the strain gauges should be fine for this application. But i need it to work in all posible probing directions.
HX711 has two channels. I might use both. But i don't know if it's good idea to use 1 strain gauge in one channel and 2 gauges in other. That might introduce inconsistent results when touching from different directions. Also i might use two and two gauges in "X" configuration, but then again i would be afraid that the can cancel each other out...
Any ideas on this one? Thanks.
Hi,
i am experimenting with various CNC touch probe designs and i've came across following setup using straingauges CA-glued to elastic frame holding the probe tip. I will probably use aluminum or acrylic as base for the strain gauge.
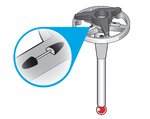
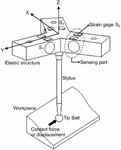
I wonder if there is a way to wire this using single instrumentation amplifier channel. (i am going to use HX711 inamp with integrated ADC).
Problem is that i am afraid that under certain angles of side load, the strain gauges can cancel each other when placed in single wheatstone bridge. Unlike personal scale (which has all strain gauges loaded in the same direction by person standing on top of it) these touch probe strain gauges will be loaded in both compression and tension randomly based on direction of touch. If this happens, the CNC will continue moving towards the probed object and break the probe. I need this to be as sensitive as possible without being affected by stepper motor vibrations and intertia of probe tips.
I don't really need to use the 3 beamed star topology showed in image. I can use any other strain gauge placement as long as it's at least kind of symetric. But i want to produce strain gauge based needle that will be sensitive to mechanical touch from any direction (both axial and radial). I can even use some kind of multiaxial strain gauge. But i am bit lost in the choices. Also they are usualy much more expensive...
I need this to work with sharp tip to have enough resolution. But i don't want to puncture the scanned object. I've tried with cheap chinese weighing scale. It's based on load cell and sensitive enough to react when i press my finger against the tip of the needle needle without puncturing my skin. So i think the strain gauges should be fine for this application. But i need it to work in all posible probing directions.
HX711 has two channels. I might use both. But i don't know if it's good idea to use 1 strain gauge in one channel and 2 gauges in other. That might introduce inconsistent results when touching from different directions. Also i might use two and two gauges in "X" configuration, but then again i would be afraid that the can cancel each other out...
Any ideas on this one? Thanks.
Last edited: