Veketti
Full Member level 3

Dear All,
I'd like to implement short circuit protection for my designs and have some doubts.. For example now I'm designing a vehicle installed meter with PIC microcontroller. From 12V to 5V I use Murata OKI-78SR-5 regulator and from that supply PIC and 5V to pressure sensor. I need short circuit protection for that 5V supply to the sensor.
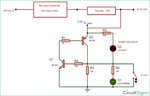
I tested this circuit and noticed that it draws too much current when on. I modified it so that changed R2 to 10k, R5 to 10k and removed D2 as I don't need any indication if shorted. Circuit worked on breadboard with BC337 and BC327 transistors. My guestion is, how do you calculate the base resistor for this kind of situations when there are many components interacting with each other? I know how to calculate it for single transistor. In my tests I had only one led representing the load. I'd like to be sure that this modification is working in calculations as well. I liked this solution as it did auto recover when short was removed.
The other thing, I will add TVS diode between supply and ground, before the murata and diode to positive side for protecting reverse polarity. Are there other things to consider?
Thank you in advance.
I'd like to implement short circuit protection for my designs and have some doubts.. For example now I'm designing a vehicle installed meter with PIC microcontroller. From 12V to 5V I use Murata OKI-78SR-5 regulator and from that supply PIC and 5V to pressure sensor. I need short circuit protection for that 5V supply to the sensor.
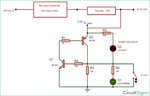
I tested this circuit and noticed that it draws too much current when on. I modified it so that changed R2 to 10k, R5 to 10k and removed D2 as I don't need any indication if shorted. Circuit worked on breadboard with BC337 and BC327 transistors. My guestion is, how do you calculate the base resistor for this kind of situations when there are many components interacting with each other? I know how to calculate it for single transistor. In my tests I had only one led representing the load. I'd like to be sure that this modification is working in calculations as well. I liked this solution as it did auto recover when short was removed.
The other thing, I will add TVS diode between supply and ground, before the murata and diode to positive side for protecting reverse polarity. Are there other things to consider?
Thank you in advance.