ctzof
Full Member level 3

Hello,
I am designing a high speed DAQ transceiver and I am in the stage of designing the stack. In the following picture you can see what Ive done already. High speed differential lines will be routed on S1, S2, S5, S3 and bottom layer TOP layer is going to be used for other lines and sps. I need a recommendation about the thickness of dielectrics of the ground and power planes. For me is it better to make them small as with this way I can reduce the total thickness of the board but what do you recommend. Which are the differences of using large and small thickness for the dielectrics in the power planes. Thanks
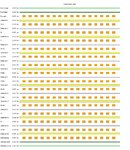
I am designing a high speed DAQ transceiver and I am in the stage of designing the stack. In the following picture you can see what Ive done already. High speed differential lines will be routed on S1, S2, S5, S3 and bottom layer TOP layer is going to be used for other lines and sps. I need a recommendation about the thickness of dielectrics of the ground and power planes. For me is it better to make them small as with this way I can reduce the total thickness of the board but what do you recommend. Which are the differences of using large and small thickness for the dielectrics in the power planes. Thanks
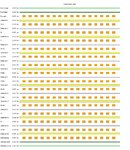
Last edited: