tuk
Junior Member level 1

fan/motor details
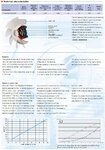
as the title suggests I am planning on using a mosfet driver to control a dc fan/motor, have no idea what kind I need to do the job, there are many different types
fan/motor will run 24/7 365 days ..possibly for several years
fan/motor will run continuously and vary between 10%-100% power
fan/motor speed will be auto controlled by an MC(Arduino/PWM) via the mosfet ......in response to temperature
if the mosfet can feedback motor info to the MC ...speed etc that would good also
1)how to choose a suitable driver: do I match the current rating of mosfet to the fan/motor current rating?
2)can I buy something off the shelf or do I have to build?
3)how exactly does the mosfet connect to the fan/motor ..is the fans power cable run through the mosfet or do I need to open up the fan housing and connect directly to the motor?
4)Are there any extra fire risks or other safety issues I have to consider?
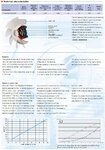
as the title suggests I am planning on using a mosfet driver to control a dc fan/motor, have no idea what kind I need to do the job, there are many different types
fan/motor will run 24/7 365 days ..possibly for several years
fan/motor will run continuously and vary between 10%-100% power
fan/motor speed will be auto controlled by an MC(Arduino/PWM) via the mosfet ......in response to temperature
if the mosfet can feedback motor info to the MC ...speed etc that would good also
1)how to choose a suitable driver: do I match the current rating of mosfet to the fan/motor current rating?
2)can I buy something off the shelf or do I have to build?
3)how exactly does the mosfet connect to the fan/motor ..is the fans power cable run through the mosfet or do I need to open up the fan housing and connect directly to the motor?
4)Are there any extra fire risks or other safety issues I have to consider?
Last edited: