zhangz64
Junior Member level 3

Hi Everyone,
I am currently struggling to determine the power supply for my board, and would really appreciate some inputs.
the Board i am designing requires a High level of precision and consist of the following sub circuits.
1) High precision Bias Voltage from DAC
2) High precision Bias Current
3) low noise Adjustable power supply.
Therefore, Minimizing noise is really important for those circuits. So Here is what i am proposing.
The board requires approximately 700mA @3.3V maximum.
Since It will not alway operate at maximum, I can power the board with a single host USB for most of the time.( I think usb 2.0 can supply for up to 500mA at 5V)
if more current is required , i will just connect another usb from a wall charger.(diode connection with the usb host).
The problem with those USB supply is that they are somewhat noisy. I do not want those noise to roam on my board, So i put a immediate LDO next to the USB input port to step it down to 4.5Vs and give me a nice clean power supply.
Here are my questions:
1) Should i use 5V to get 4.5V from master LDO and then use separate LDOs to get 3.3V for each sub circuit(picture 1) ? or does it make a difference to have 5V directly down to 3.3Vs shared for all the sub circuit(picture 2).
2)DO i really need an additional USB supply from wall charger? or A single host usb is enough ? Does my calculation make sense?
( 5V * 500mA / 3.3V = 750mA, and some losses of course from LDO).
3) What other things i should be considering to minimize the noise? (etc,separate digital supply from analog supply ?, layout consideration)
Thanks a lot for the help,
Eddy
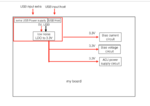
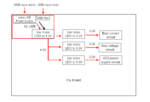
I am currently struggling to determine the power supply for my board, and would really appreciate some inputs.
the Board i am designing requires a High level of precision and consist of the following sub circuits.
1) High precision Bias Voltage from DAC
2) High precision Bias Current
3) low noise Adjustable power supply.
Therefore, Minimizing noise is really important for those circuits. So Here is what i am proposing.
The board requires approximately 700mA @3.3V maximum.
Since It will not alway operate at maximum, I can power the board with a single host USB for most of the time.( I think usb 2.0 can supply for up to 500mA at 5V)
if more current is required , i will just connect another usb from a wall charger.(diode connection with the usb host).
The problem with those USB supply is that they are somewhat noisy. I do not want those noise to roam on my board, So i put a immediate LDO next to the USB input port to step it down to 4.5Vs and give me a nice clean power supply.
Here are my questions:
1) Should i use 5V to get 4.5V from master LDO and then use separate LDOs to get 3.3V for each sub circuit(picture 1) ? or does it make a difference to have 5V directly down to 3.3Vs shared for all the sub circuit(picture 2).
2)DO i really need an additional USB supply from wall charger? or A single host usb is enough ? Does my calculation make sense?
( 5V * 500mA / 3.3V = 750mA, and some losses of course from LDO).
3) What other things i should be considering to minimize the noise? (etc,separate digital supply from analog supply ?, layout consideration)
Thanks a lot for the help,
Eddy
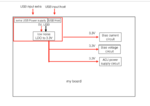
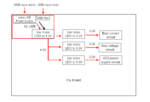