deepmak
Member level 2

greetings all
i'm trying to make an input module for a micro controller circuit that monitor the status of multiple switches (NC/NO) , the input module should be able to deal with both type of switches without the need of changing the PIC programming.
i tried to solve this using optocoupler since the switches are connected to 24VDC to 27.5 VDC (batteries with charger ), the output of the optocoupler is connected to an inverter , the input of the PIC pin can be selected using a jumper according to the normal operation mode of the switch (No or NC )
could you please check the attached photo and advise if any other consideration i should make , the micro controller and 24 VDC will share same ground.
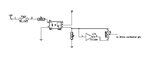
also i was checking online , any of you used the 6N137 optocoupler ? can it serve for the same function using the jumper to apply 5 v or 0v at the enable pin ? and would it be better to use the 6N137 this way to make less complicated PCB ?
thanks in advance
Regards
i'm trying to make an input module for a micro controller circuit that monitor the status of multiple switches (NC/NO) , the input module should be able to deal with both type of switches without the need of changing the PIC programming.
i tried to solve this using optocoupler since the switches are connected to 24VDC to 27.5 VDC (batteries with charger ), the output of the optocoupler is connected to an inverter , the input of the PIC pin can be selected using a jumper according to the normal operation mode of the switch (No or NC )
could you please check the attached photo and advise if any other consideration i should make , the micro controller and 24 VDC will share same ground.
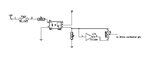
also i was checking online , any of you used the 6N137 optocoupler ? can it serve for the same function using the jumper to apply 5 v or 0v at the enable pin ? and would it be better to use the 6N137 this way to make less complicated PCB ?
thanks in advance
Regards
Last edited: