Noob_tronic
Newbie level 4

Hello,
To attain a good understanding of necessaries knowledges to drive IGBT and Mosfets is a goal. This way allows me to upgrade electromechanical skills.
The to do list practical projects consist to make :
- Pure sine wave inverter with a driver piloted with pwm micro controller outputs.
- Drive the speed of an asynchronous machine
- An induction forging
- An IGBT/Mosfet Current-Regulation
For information I’ve electrician certifications, but I really try to be humble with electric shocks and the death risk. We will never be reiterated enough that the Electricity is potentially mortal.
The simple first project that I would like to design is the induction forge, because I suppose it’s easiest to make a circuit with a single IGBT to reduce the risk to burn half bridge transistors. The “single low-side driver” design is the purpose of this post.
To discover IR2110 Mosfet/IGBT driver specifications was an adventure. This blog description looks good : http://archive.is/xzSIY . But for the moment I’haven’t got Mosfet and I use IGBT.
Measurements and tests allow me to understand the “IR2110 driver” basic specifications, with the “single low-side driver” design. “LIN input” take a “5V_30kHz_ 50% duty” signal. “VCC input” has a large variable adjusting range from 10 to 18V, with a fixed value for “VDD input” at 9,05V. That design allow me to create a “LO output” tension between 3V to 6V at 30kHz for “GT50N322A” IGBT.
http://www.datasheets360.com/pdf/-6226261397393676843
Unless if I mistaken “LO output” is the threshold/VGE tension which drives the IGBT ON/OFF. To limit IGBT explosion risks, and also try to regulate the current, I made the choice to connect an 40ohm oven resistor with 325V DC “between +circuit and the IGBT collector”. With that design the short circuit with a potential semiconductor explosion should be limited.
When I connected the “GT50N322A” nothing was working ; I suppose that the current driver wasn’t enough to switch this IGBT. I also asked myself about the necessity to connect a diode between emitter/collector and maybe a capacitor ? Unfortunately, I maybe destroyed the ninth IGBT, which was the second to last ; but I don’t know ?
Then I tried to drive the last IGBT with just the “PMW microcontroller output” and an “optocopler TLP521-2”. When I passed 5.5V_30kHz_50%_duty on the gate, the IGBT was conducting 8Amp, but it wasn’t possible to cut off the circuit. A 10kohms resistor was connected between the “Gate and the Emitter”, and a diode between “Emitter and Collector”. I used a 10ohms resistor between the “optocopler output” and the “IGBT gate”.
My questions :
- To plug a MKP capacitor between Emitter and Collector as the “AV R76 MKP” 100nF is maybe the solution ?
- What the difference between a Mosfet drive and an IGBT control ?
- How we can control current in the IGBT ? A current limitation on the gate, or, a VGE tension regulation ?
- Why the data-sheet specification precises VGE tension between 3V and 6V, unless if the Ic(A) f (VGE) curves allow between 7 and 8V ?
- Did I destroyed all this expensives IGBT ?
Thank you for your time and answers.
Nico
:-?
Using the IR2110 as a single low-side driver from tahmidmc.blogspot.com
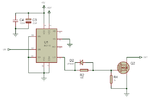
IR2110 Logic "1" Input Threshold vs VDD
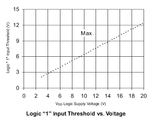
To attain a good understanding of necessaries knowledges to drive IGBT and Mosfets is a goal. This way allows me to upgrade electromechanical skills.
The to do list practical projects consist to make :
- Pure sine wave inverter with a driver piloted with pwm micro controller outputs.
- Drive the speed of an asynchronous machine
- An induction forging
- An IGBT/Mosfet Current-Regulation
For information I’ve electrician certifications, but I really try to be humble with electric shocks and the death risk. We will never be reiterated enough that the Electricity is potentially mortal.
The simple first project that I would like to design is the induction forge, because I suppose it’s easiest to make a circuit with a single IGBT to reduce the risk to burn half bridge transistors. The “single low-side driver” design is the purpose of this post.
To discover IR2110 Mosfet/IGBT driver specifications was an adventure. This blog description looks good : http://archive.is/xzSIY . But for the moment I’haven’t got Mosfet and I use IGBT.
Measurements and tests allow me to understand the “IR2110 driver” basic specifications, with the “single low-side driver” design. “LIN input” take a “5V_30kHz_ 50% duty” signal. “VCC input” has a large variable adjusting range from 10 to 18V, with a fixed value for “VDD input” at 9,05V. That design allow me to create a “LO output” tension between 3V to 6V at 30kHz for “GT50N322A” IGBT.
http://www.datasheets360.com/pdf/-6226261397393676843
Unless if I mistaken “LO output” is the threshold/VGE tension which drives the IGBT ON/OFF. To limit IGBT explosion risks, and also try to regulate the current, I made the choice to connect an 40ohm oven resistor with 325V DC “between +circuit and the IGBT collector”. With that design the short circuit with a potential semiconductor explosion should be limited.
When I connected the “GT50N322A” nothing was working ; I suppose that the current driver wasn’t enough to switch this IGBT. I also asked myself about the necessity to connect a diode between emitter/collector and maybe a capacitor ? Unfortunately, I maybe destroyed the ninth IGBT, which was the second to last ; but I don’t know ?
Then I tried to drive the last IGBT with just the “PMW microcontroller output” and an “optocopler TLP521-2”. When I passed 5.5V_30kHz_50%_duty on the gate, the IGBT was conducting 8Amp, but it wasn’t possible to cut off the circuit. A 10kohms resistor was connected between the “Gate and the Emitter”, and a diode between “Emitter and Collector”. I used a 10ohms resistor between the “optocopler output” and the “IGBT gate”.
My questions :
- To plug a MKP capacitor between Emitter and Collector as the “AV R76 MKP” 100nF is maybe the solution ?
- What the difference between a Mosfet drive and an IGBT control ?
- How we can control current in the IGBT ? A current limitation on the gate, or, a VGE tension regulation ?
- Why the data-sheet specification precises VGE tension between 3V and 6V, unless if the Ic(A) f (VGE) curves allow between 7 and 8V ?
- Did I destroyed all this expensives IGBT ?
Thank you for your time and answers.
Nico
:-?
Using the IR2110 as a single low-side driver from tahmidmc.blogspot.com
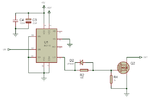
IR2110 Logic "1" Input Threshold vs VDD
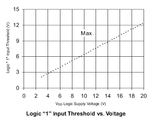