rmanalo
Advanced Member level 4

- Joined
- Feb 8, 2017
- Messages
- 107
- Helped
- 16
- Reputation
- 32
- Reaction score
- 16
- Trophy points
- 18
- Location
- Philippines
- Activity points
- 979
Hello everyone,
I've read that trimming is a post-fabrication adjustment technique, but I like to show the trimming method through simulation using only ideal switches for now. I've been struggling with trimming my voltage reference in simulation in the SS corner. The first try I tried to use a simple ideal switch shown.
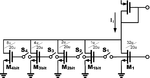
I used a g-element in hspice to model the switch, the voltage-controlled-resistor varies from a minimum of 100u-ohm to 100g-ohm. The results have no change because at open circuit (100g-ohm) there is still a connection.
The second try I used a path selector as shown
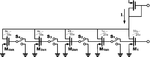
Still using g-element switch model for the two swtiches, the results were unsatisfactory (400ppm/C instead of 80ppm by independently adding parallel transistors at SS Corner).
The last one is not a digital trimming method as it uses fuses as shown
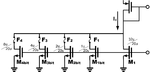
So far this is my best option but I cant simulate a fuse in hspice.
From here I have a few questions
1. are there any more methods for me to try? What are good references or books that tackle and explain digital trimming in detail, such as a full circuit
2. I used ideal switches in this case, it makes me wonder if implementing this as a circuit will have worse results
3. Is implementing fuses a good idea for a 4 bit trim range? (concerning on the number of trimming pads)
I've read that trimming is a post-fabrication adjustment technique, but I like to show the trimming method through simulation using only ideal switches for now. I've been struggling with trimming my voltage reference in simulation in the SS corner. The first try I tried to use a simple ideal switch shown.
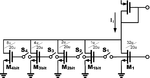
I used a g-element in hspice to model the switch, the voltage-controlled-resistor varies from a minimum of 100u-ohm to 100g-ohm. The results have no change because at open circuit (100g-ohm) there is still a connection.
The second try I used a path selector as shown
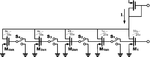
Still using g-element switch model for the two swtiches, the results were unsatisfactory (400ppm/C instead of 80ppm by independently adding parallel transistors at SS Corner).
The last one is not a digital trimming method as it uses fuses as shown
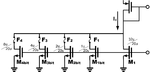
So far this is my best option but I cant simulate a fuse in hspice.
From here I have a few questions
1. are there any more methods for me to try? What are good references or books that tackle and explain digital trimming in detail, such as a full circuit
2. I used ideal switches in this case, it makes me wonder if implementing this as a circuit will have worse results
3. Is implementing fuses a good idea for a 4 bit trim range? (concerning on the number of trimming pads)