khansaab21
Advanced Member level 4

Hello guys, following is my circuit representing a single phase of a three phase inverter for driving a three phase AC induction motor.
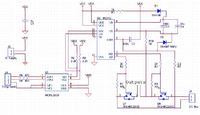
The isolators are reproducing the PWM inputs nice and smooth. Low side is running good. Low side is driving the load as intended. (I have tested it using DC motor as a load connected between collector of low IGBT and Vcc and the speed was varying proportional to PWM).
The problem relies with the high side. It is not driving the load AT ALL. Following are some of the facts that I can observe in the circuit. High side supply is 15V and low side is 12V. The input is PWM at 20kHz. The output is between emitter of high side IGBT and ground.
1. VB pin doesnt go beyond 12V.
2. HO pin carries 10V, at no load condition.
3. HO pin drops to 0.8 V as soon as load gets connected.
Is there a problem in the circuit or I am missing something??
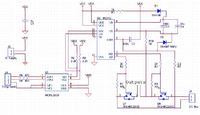
The isolators are reproducing the PWM inputs nice and smooth. Low side is running good. Low side is driving the load as intended. (I have tested it using DC motor as a load connected between collector of low IGBT and Vcc and the speed was varying proportional to PWM).
The problem relies with the high side. It is not driving the load AT ALL. Following are some of the facts that I can observe in the circuit. High side supply is 15V and low side is 12V. The input is PWM at 20kHz. The output is between emitter of high side IGBT and ground.
1. VB pin doesnt go beyond 12V.
2. HO pin carries 10V, at no load condition.
3. HO pin drops to 0.8 V as soon as load gets connected.
Is there a problem in the circuit or I am missing something??