hm_fa_da
Full Member level 5

Hi,
I'm designing a device which connects to two Gas volume converter at same time to read out them by RS232 port.
Converter like Actaris Corus are completely Isolated by optocouplers and won't have problem.
But Converters like Elster EK220 RS232 Port is not electrically isolated from the main board ( the main board is connected to temp and pressure sensors ...)
Note all devices are battery powered separately. My device must supply 9V power for EK220 RS232 ports when connecting to it.
the schematic is like below:
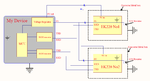
Each device has it's own Battery as you see in schematic. but my device should power up conerters 9V input when connecting to them.
In Ek220, you see 10M resistor which is connected between 0V of main board and Aluminum box of it.
In my design, i doubt maybe there is a problem in design and some risks against ATEX considerations !
What's your suggestion ?
is this diagram okay ? or i have to use both power supply isolaters and optocouplers for TXD-RXD lines ?
I know in these devices sometimes barriers are used, but they are usually used when device is externally powered from i.e 220 to 9V or RS232 port is connecting to a device which has 220V inside.
I'm designing a device which connects to two Gas volume converter at same time to read out them by RS232 port.
Converter like Actaris Corus are completely Isolated by optocouplers and won't have problem.
But Converters like Elster EK220 RS232 Port is not electrically isolated from the main board ( the main board is connected to temp and pressure sensors ...)
Note all devices are battery powered separately. My device must supply 9V power for EK220 RS232 ports when connecting to it.
the schematic is like below:
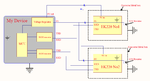
Each device has it's own Battery as you see in schematic. but my device should power up conerters 9V input when connecting to them.
In Ek220, you see 10M resistor which is connected between 0V of main board and Aluminum box of it.
In my design, i doubt maybe there is a problem in design and some risks against ATEX considerations !
What's your suggestion ?
is this diagram okay ? or i have to use both power supply isolaters and optocouplers for TXD-RXD lines ?
I know in these devices sometimes barriers are used, but they are usually used when device is externally powered from i.e 220 to 9V or RS232 port is connecting to a device which has 220V inside.