lucasromeiro
Newbie level 5

Hello guys.
I'm using an efr32bg22 Bluetooth module and would like to read a thermistor with it!
I've never used a thermistor.
Reading a little about the subject, it seems a little complicated to me.
There are some formulas for obtaining a conversion but apparently the best way is to use a conversion table.
Unfortunately I don't know how to do any of them.
I would like to use the table or a method that helps to have greater precision.
I bought 2 thermistor models and I have them here with me:
NTCSP103JF103FT1S
TX06F103F3435ER
I had a temperature sensor that used a thermistor to measure the temperature inside a refrigerator. I want to do the same thing.
I disassembled the sensor and the circuit I found was as follows:
I imagine that I can replicate this circuit, but the part of converting the ADC signal to the temperature accurately I still don't know how to do it.
Can someone help me?
Important: I intend to use the range from 30 to -40 degrees celcius.
Most of the time it will operate in the range of 10 to -20 degrees celcius (inside a fridge or freezer).
Can anyone help me with this?
I'm using an efr32bg22 Bluetooth module and would like to read a thermistor with it!
I've never used a thermistor.
Reading a little about the subject, it seems a little complicated to me.
There are some formulas for obtaining a conversion but apparently the best way is to use a conversion table.
Unfortunately I don't know how to do any of them.
I would like to use the table or a method that helps to have greater precision.
I bought 2 thermistor models and I have them here with me:
NTCSP103JF103FT1S
TX06F103F3435ER
I had a temperature sensor that used a thermistor to measure the temperature inside a refrigerator. I want to do the same thing.
I disassembled the sensor and the circuit I found was as follows:
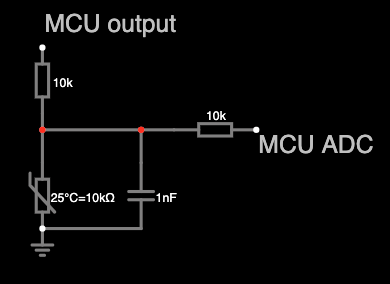
I imagine that I can replicate this circuit, but the part of converting the ADC signal to the temperature accurately I still don't know how to do it.
Can someone help me?
Important: I intend to use the range from 30 to -40 degrees celcius.
Most of the time it will operate in the range of 10 to -20 degrees celcius (inside a fridge or freezer).
Can anyone help me with this?