gres
Full Member level 4

Cheap milling machine.
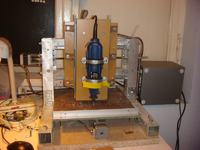
Project is based on few similar from cnc-info.
Frame of construction is cut to pieces aluminum profile 4x4cm. it's food is particleboard 22mm. All is tight by screws and angles. For providers I used classic taken from drawer.
Drive is a screw bar M8 with steal nuts. Soon I will replace them by brass sleeves with trapezoidal thread. Right now machine has speed about 600mm/min.
System is taken from linux-cnc.org. it's very friendly and has a lot of conveniences like EMC2 program. It's steering through step/ direction comments that comes via LPT port. I used that in my drivers.
While I was reading L297 manual i found interesting thing - how the step motor should be controlled in HalfStep mode. Thanks to that engines are smooth and they have much bigger torque. Atmeg8 is responsible for proper work. Power transistors has supply so can steer current 4A per phase.
Next step was chopper for step motors. Phase winding those engines have tendencies to increase impedance when speed is increasing. That's why current that flows throught windings is lower so torque is smaller. To avoid this we need bigger power voltage and current is limited by chooper that forced rated current at winding. My system is not a typical chooper because doesn't use DC/DC converter but LM317 chipsets. I put current limiter - 1,5A and power 30V.
Tool work's fine but i'm going to remove providers and replace them by those with fi16 shaft and bearings. Also drive should be exchanged to trapezoidal screws.
More information are here: https://www.elektroda.pl/rtvforum/topic1532487.html
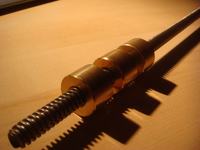
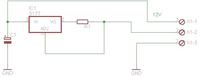
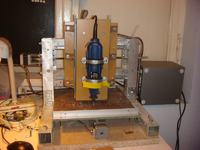
Project is based on few similar from cnc-info.
Frame of construction is cut to pieces aluminum profile 4x4cm. it's food is particleboard 22mm. All is tight by screws and angles. For providers I used classic taken from drawer.
Drive is a screw bar M8 with steal nuts. Soon I will replace them by brass sleeves with trapezoidal thread. Right now machine has speed about 600mm/min.
System is taken from linux-cnc.org. it's very friendly and has a lot of conveniences like EMC2 program. It's steering through step/ direction comments that comes via LPT port. I used that in my drivers.
While I was reading L297 manual i found interesting thing - how the step motor should be controlled in HalfStep mode. Thanks to that engines are smooth and they have much bigger torque. Atmeg8 is responsible for proper work. Power transistors has supply so can steer current 4A per phase.
Next step was chopper for step motors. Phase winding those engines have tendencies to increase impedance when speed is increasing. That's why current that flows throught windings is lower so torque is smaller. To avoid this we need bigger power voltage and current is limited by chooper that forced rated current at winding. My system is not a typical chooper because doesn't use DC/DC converter but LM317 chipsets. I put current limiter - 1,5A and power 30V.
Tool work's fine but i'm going to remove providers and replace them by those with fi16 shaft and bearings. Also drive should be exchanged to trapezoidal screws.
More information are here: https://www.elektroda.pl/rtvforum/topic1532487.html
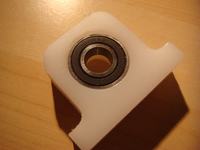
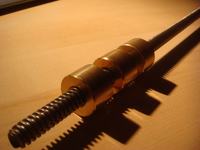
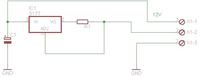