Tomsin yin
Banned

hi guys
currently am designing a power divider with its frequency range 2~3Ghz,and i used a block of microtrip board with its Er=2.65,H=1mm,i had printed the PCB and did the hardware circuit for three blocks,but S11 is very weak,it is only about 10dB(but S11 is more than 20dB in my co-simulation),so i asked my adviser that why my S11 is so lousy,he said nothing but told me not to corrosin microstip board.so i wanna know why microstip board can't be corrosined?could anybody answer me ?
its grateful for ur replys.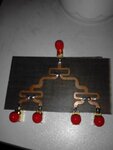
currently am designing a power divider with its frequency range 2~3Ghz,and i used a block of microtrip board with its Er=2.65,H=1mm,i had printed the PCB and did the hardware circuit for three blocks,but S11 is very weak,it is only about 10dB(but S11 is more than 20dB in my co-simulation),so i asked my adviser that why my S11 is so lousy,he said nothing but told me not to corrosin microstip board.so i wanna know why microstip board can't be corrosined?could anybody answer me ?
its grateful for ur replys.
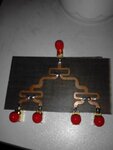