BenzT
Junior Member level 3

Hi,
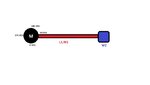
Object with a weight of W2 kg has to be moved and positioned at any degrees from 0 to 360. So i used a arm with a length L1 and weight W1 to carry the object.
I am not rotating parallel to the floor or ground. Its against the gravity like a giant wheel...
How do i select a motor based on some or all of the given parameters ( Torque,Gear Ratio,Power On...)
Pls give any formulas, Weblinks, Documents to know the details about it...
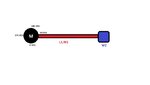
Object with a weight of W2 kg has to be moved and positioned at any degrees from 0 to 360. So i used a arm with a length L1 and weight W1 to carry the object.
I am not rotating parallel to the floor or ground. Its against the gravity like a giant wheel...
How do i select a motor based on some or all of the given parameters ( Torque,Gear Ratio,Power On...)
Pls give any formulas, Weblinks, Documents to know the details about it...