tiwari.sachin
Full Member level 6

Let me first explain the requirement.
There shall be 2 options to power this board. First from SMPS (12V, 3 amps) or a car battery (12V).
Second via a Li Ion battery (2 cell, 7.4V, 4000mAH)
The battery charging and switching between SMPS or a Li Ion Battery is working and is tested.
The below block shall give the complete details.
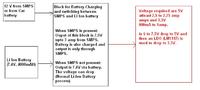
I tried using LM2576 for 5v and 1117 for 3.3V and during test, when I connect a load that draws about 1amp on 5V, LM2576 heats up. I have not connected any load on 3.3V.
If in case there is no SMPS and the power to this module is via Li Ion Battery then the voltage on this battery will drop and this should not have issues with output voltage.
My observations are that when the input voltage drops below 7.4V, the output of the LM2576 will also start to drop and this obviously is not intended.
I am planning to use a LDO for 5V also instead of LM2576.
Do suggest me if I am doing it the right way or is my concept wrong.
Below is how I am taking care of charging:
1. Drop from 12V SMPS to 7.5V using diodes. (This is not a good option as it takes lot of diodes to do so). I am doing it so that I keep same voltage as input for LM2576.
2. Switching between SMPS and battery is done using MOSFET. I am checking if SMPS power is present, if it is then the power is from SMPS and if not then via battery.
3. When the SMPS is present, the LiIon Battery is charged and it draws about 500mA during charging. After charging is completed, it disconnects itself and power flow is via SMPS as long as it is present. I am using BQ24105 from TI for charging.
My concerns are that the SMPS and Li Ion battery is decided by the customer and he wants it to be same and cannot be changed. Suggestions on changing the battery or input is not possible.
He has a new requirement now that says that the module could also be used in vehicle and hence instead of SMPS, he can connect that to a car battery too... So now the components have to be automotive grade too.
Do share your views on this design and flow.
There shall be 2 options to power this board. First from SMPS (12V, 3 amps) or a car battery (12V).
Second via a Li Ion battery (2 cell, 7.4V, 4000mAH)
The battery charging and switching between SMPS or a Li Ion Battery is working and is tested.
The below block shall give the complete details.
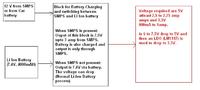
I tried using LM2576 for 5v and 1117 for 3.3V and during test, when I connect a load that draws about 1amp on 5V, LM2576 heats up. I have not connected any load on 3.3V.
If in case there is no SMPS and the power to this module is via Li Ion Battery then the voltage on this battery will drop and this should not have issues with output voltage.
My observations are that when the input voltage drops below 7.4V, the output of the LM2576 will also start to drop and this obviously is not intended.
I am planning to use a LDO for 5V also instead of LM2576.
Do suggest me if I am doing it the right way or is my concept wrong.
Below is how I am taking care of charging:
1. Drop from 12V SMPS to 7.5V using diodes. (This is not a good option as it takes lot of diodes to do so). I am doing it so that I keep same voltage as input for LM2576.
2. Switching between SMPS and battery is done using MOSFET. I am checking if SMPS power is present, if it is then the power is from SMPS and if not then via battery.
3. When the SMPS is present, the LiIon Battery is charged and it draws about 500mA during charging. After charging is completed, it disconnects itself and power flow is via SMPS as long as it is present. I am using BQ24105 from TI for charging.
My concerns are that the SMPS and Li Ion battery is decided by the customer and he wants it to be same and cannot be changed. Suggestions on changing the battery or input is not possible.
He has a new requirement now that says that the module could also be used in vehicle and hence instead of SMPS, he can connect that to a car battery too... So now the components have to be automotive grade too.
Do share your views on this design and flow.