Jestin_cubetech
Advanced Member level 1

AC lamp dimmer using MOSFET PWM
AC lamp dimmer using MOSFET PWM.
circuit diagram
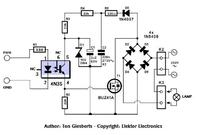
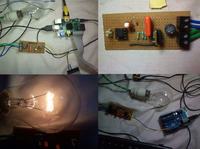
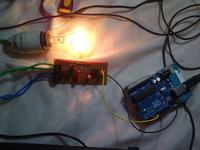
https://www.youtube.com/watch?v=P8lGGEnO488
https://www.youtube.com/watch?v=o4o2ztiD2UY
https://www.instructables.com/id/safe-and-simple-AC-PWM-Dimmer-for-arduino-Raspberr/
AC lamp dimmer using MOSFET PWM.
circuit diagram
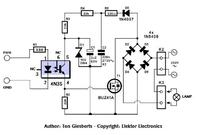
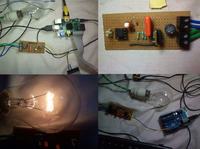
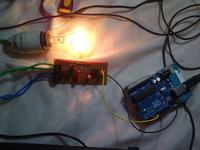
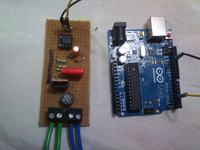
https://www.youtube.com/watch?v=P8lGGEnO488
https://www.youtube.com/watch?v=o4o2ztiD2UY
https://www.instructables.com/id/safe-and-simple-AC-PWM-Dimmer-for-arduino-Raspberr/