david.cano90
Junior Member level 3

Hello everyone,
I am designing a current transformer (CT) to sense the current that is flowing in every single switch for a DC-DC converter.
The converter is going to be built through a push-pull topology, and it has to deliver 200 W @200V. The input voltage is 24 V.
The MOSFETs that I chose can deal up to 50 A.
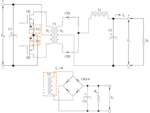
(Image taken from: McLyman, C. W. T. (2011). Transformer and Inductor Design Handbook, Fourth Edition. CRC Press.)
Following Mclyman's procedure, I got this:
The peak current that I want to measure for making the Current Mode Control (CMC) is 45 A.
The primary has 1 turn and the the secondary 150. In the secondary I would have 0.3 A. The load of the CT is 2.5 Ohm.
The voltage that I am willing to have when the peak current arises is 0.75 at the secondary of the CT (for the CMC).
I am afraid of the magnetizing current and the losses of the CT.
What do you think about the design? Could the CT work for measuring that amount of current?
If there are troubles, could you please give me a hint or something?
As always, thank you for reading.
I would appreciate your help.
Have a nice day!
David.
I am designing a current transformer (CT) to sense the current that is flowing in every single switch for a DC-DC converter.
The converter is going to be built through a push-pull topology, and it has to deliver 200 W @200V. The input voltage is 24 V.
The MOSFETs that I chose can deal up to 50 A.
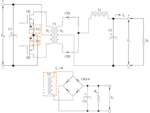
(Image taken from: McLyman, C. W. T. (2011). Transformer and Inductor Design Handbook, Fourth Edition. CRC Press.)
Following Mclyman's procedure, I got this:
The peak current that I want to measure for making the Current Mode Control (CMC) is 45 A.
The primary has 1 turn and the the secondary 150. In the secondary I would have 0.3 A. The load of the CT is 2.5 Ohm.
The voltage that I am willing to have when the peak current arises is 0.75 at the secondary of the CT (for the CMC).
I am afraid of the magnetizing current and the losses of the CT.
What do you think about the design? Could the CT work for measuring that amount of current?
If there are troubles, could you please give me a hint or something?
As always, thank you for reading.
I would appreciate your help.
Have a nice day!
David.