darkwingduck
Newbie level 6

- Joined
- Aug 4, 2015
- Messages
- 12
- Helped
- 0
- Reputation
- 0
- Reaction score
- 0
- Trophy points
- 1
- Activity points
- 90
hi guys please help im new to this
i need to make this...
it is a adapter for my 3ds to use a gamecube controller
i can get all the parts needed except the "board" in the instructions the guy said for the board i will have to find a way to make it. my question is can i use this ( since this is what i can buy )
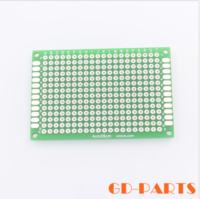
in order to make this
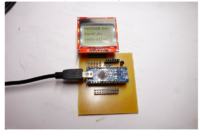
this is what he used
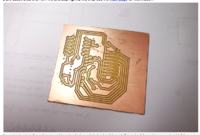
i need to make this...
it is a adapter for my 3ds to use a gamecube controller
i can get all the parts needed except the "board" in the instructions the guy said for the board i will have to find a way to make it. my question is can i use this ( since this is what i can buy )
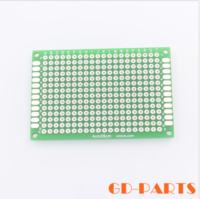
in order to make this
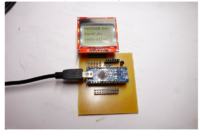
this is what he used
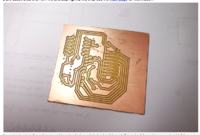