nirmit27
Junior Member level 3

- Joined
- Jun 20, 2016
- Messages
- 30
- Helped
- 0
- Reputation
- 0
- Reaction score
- 0
- Trophy points
- 6
- Activity points
- 248
I2C Communication for Honeywell pressure sensor
Hi
I am using Honeywell pressure sensor to measure pressure of air in a pipe.
for this have to use I2C Communication with pic PIC16F1787
circuit for this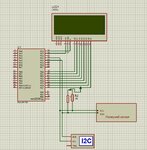
is my Circuit is perfect ? Help me out
in programming side i used I2C protocol
for Honeywell air pressure sensor's Digital I2C address is 0X49.
to reading data from sensor
the program flow are 1st master send data to slave
>send start condition
> send Digital address (0X48)
> stop condition
2ndly read data from slave means slave response to master
> start condition
> Digital address (0x49)
> than reading data
moreover for same program for RTC DS1307 slave
i am getting data from RTC with RTC address in same program but i am not even getting garbage value for Honeywell sensor for same I2C pin and configuration
so is there any programming change for this particular sensor
is there any additional change for this sensor for I2C protocol programming
Data sheet of Honeywell sensor is
https://sensing.honeywell.com/honey...ow-10-slpm-300-slpm-datasheet-008268-5-en.pdf
please help me out
--
Thank You
Er. Nirmit Patel
9925789327
Hi
I am using Honeywell pressure sensor to measure pressure of air in a pipe.
for this have to use I2C Communication with pic PIC16F1787
circuit for this
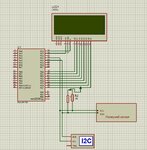
is my Circuit is perfect ? Help me out
in programming side i used I2C protocol
for Honeywell air pressure sensor's Digital I2C address is 0X49.
to reading data from sensor
the program flow are 1st master send data to slave
>send start condition
> send Digital address (0X48)
> stop condition
2ndly read data from slave means slave response to master
> start condition
> Digital address (0x49)
> than reading data
moreover for same program for RTC DS1307 slave
i am getting data from RTC with RTC address in same program but i am not even getting garbage value for Honeywell sensor for same I2C pin and configuration
so is there any programming change for this particular sensor
is there any additional change for this sensor for I2C protocol programming
Data sheet of Honeywell sensor is
https://sensing.honeywell.com/honey...ow-10-slpm-300-slpm-datasheet-008268-5-en.pdf
please help me out
--
Thank You
Er. Nirmit Patel
9925789327