magneticflux26
Newbie level 4

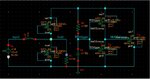
This is my proposed circuit for and ESD protection circuit. This is just a test circuit so I used
a load resistance first instead of the actual rectifier block. I did not place any Vdd since I
have read that it is the ESD voltage that biases the inverter circuit. Does this mean that the vdd
pin is floating?
I will really appreciate your insights! Thank you!