NuNDoe
Junior Member level 1
I have a strobing LED that is controlled by a microcontroller via an N MOSFET. The strobing LED is carrying a modulated signal. The microcontroller will pulse the gate voltage of the MOSFET to turn the LED on and off. (see picture)
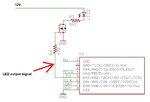
A new design requires this LED to have adjustable intensity. Since the LED has a modulated signal, using the common PWM way of dimming won't work. I will have to dim by limiting the amount of current pumping through the LED.
I thought one way to do this is to give a lower voltage to the MOSFET gate --- the lower gate voltage would be the output of a digital voltage divider. However, I don't think I will be able to get the fine tuning of current needed with a MOSFET.
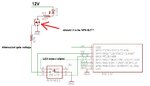
Can anyone give me some tips for my new circuit? Should I be using a PNP BJT instead of a MOSFET? If so, what are some calculations I need to perform in order to figure out what voltage needs to come out of the voltage divider and onto the base? I am using a digital potentiometer in the new design so that the microcontroller can control the output intensity.
Any advice would be greatly appreciated.
Thanks!
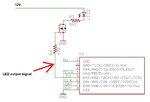
A new design requires this LED to have adjustable intensity. Since the LED has a modulated signal, using the common PWM way of dimming won't work. I will have to dim by limiting the amount of current pumping through the LED.
I thought one way to do this is to give a lower voltage to the MOSFET gate --- the lower gate voltage would be the output of a digital voltage divider. However, I don't think I will be able to get the fine tuning of current needed with a MOSFET.
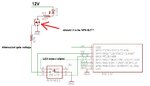
Can anyone give me some tips for my new circuit? Should I be using a PNP BJT instead of a MOSFET? If so, what are some calculations I need to perform in order to figure out what voltage needs to come out of the voltage divider and onto the base? I am using a digital potentiometer in the new design so that the microcontroller can control the output intensity.
Any advice would be greatly appreciated.
Thanks!