codemaster11
Advanced Member level 4

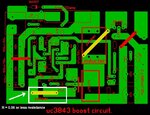
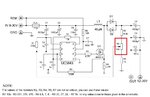
the input to the circuit is Vin = 9vdc. output of the converter is 48vdc but the regulator trimmer is not working.
connecting the trimmer with the Vfeb pin#2 of the oscillator stop the oscillator with no output voltage. disconnecting the trimmer
oscillator starts with Vout = 48vdc. i use a jumper instead the current sense resistor with resistance less than 0.06ohm.
as indicated by arrow in the pcblayout. is it the problem with jumper at the source of the MOSFET?