francis29
Member level 5

Hi guys,
i have designed a transformer for flyback converter.
I am listing all specs please check it is okey or not.
thanks in advance.
Power supply input: 100V-150V
Output 1 : 20V/1A
Output 2 : 18V/0.1A
Output 3 : 12/1A
Total Output power : 35.58Watts
Efficiency : 90%
Max duty Cycle : 30%
Output diode voltage drop : 0.85V
switching frequency : 65KHz
Primary inductance : 148.83uH
Core : EE25/13/7 Epcos Gapped
Core : material N87
Gap : 0.25mm
Al value : 250nH
Current density : 4A/mm2
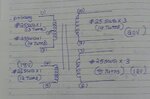
i have designed a transformer for flyback converter.
I am listing all specs please check it is okey or not.
thanks in advance.
Power supply input: 100V-150V
Output 1 : 20V/1A
Output 2 : 18V/0.1A
Output 3 : 12/1A
Total Output power : 35.58Watts
Efficiency : 90%
Max duty Cycle : 30%
Output diode voltage drop : 0.85V
switching frequency : 65KHz
Primary inductance : 148.83uH
Core : EE25/13/7 Epcos Gapped
Core : material N87
Gap : 0.25mm
Al value : 250nH
Current density : 4A/mm2
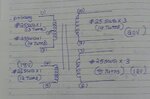