srijan.rio
Member level 2

Hello everyone.
I wanted some help regarding the design of a helix with a square cross section.
I intend to simulate an electromagnet dipole with a rectangular cross section ferrite core in HFSS(or Maxwell)
Is there any library model like the user defined primitive segmented helix? If not any suggestions as to how may I approach it would be really helpful.
Thanks
- - - Updated - - -
I was wondering whether maybe using circular helix would do with the core being rectangular and not designing the coils being wounded exactly to the sides cuboid core structure. Would it effect the simulations very much ? Apologies for my ignorance as its my first time of designing such structure. Any help will be greatly appreciated
- - - Updated - - -
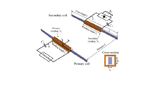
I have attached a picture of the type of winding I am talking about
I wanted some help regarding the design of a helix with a square cross section.
I intend to simulate an electromagnet dipole with a rectangular cross section ferrite core in HFSS(or Maxwell)
Is there any library model like the user defined primitive segmented helix? If not any suggestions as to how may I approach it would be really helpful.
Thanks
- - - Updated - - -
I was wondering whether maybe using circular helix would do with the core being rectangular and not designing the coils being wounded exactly to the sides cuboid core structure. Would it effect the simulations very much ? Apologies for my ignorance as its my first time of designing such structure. Any help will be greatly appreciated
- - - Updated - - -
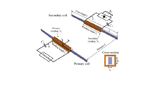
I have attached a picture of the type of winding I am talking about
Last edited: