jeolex
Member level 2

Hello my friends,
I am an academician in Department of Agriculture and I aim to make growth chambers for plants which have light, airconditioning (with computer fan) etc.. One of the important thing is light intensity of chambers. So I use 9 pcs, 3W power led for one chamber and adjust the light intensity with LM350 - potentiometer system (circle below). Leds run with 3-5V and max current is 700 mA.
I use 12 V 16A power supply. As LM350 system, Vout is approximately 11.34 V. It is ok for me and I can also adjust light intensity with potentiometer. Just problem that when I run power leds, I get 8.4 V instead of 11.34V. So this is reduce the max. light intensity. If I run power leds without LM350 system, I get 10 V and it is enough for me. You will see my circle at below. I need your helps.
Thanks..
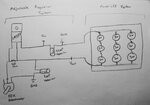
I am an academician in Department of Agriculture and I aim to make growth chambers for plants which have light, airconditioning (with computer fan) etc.. One of the important thing is light intensity of chambers. So I use 9 pcs, 3W power led for one chamber and adjust the light intensity with LM350 - potentiometer system (circle below). Leds run with 3-5V and max current is 700 mA.
I use 12 V 16A power supply. As LM350 system, Vout is approximately 11.34 V. It is ok for me and I can also adjust light intensity with potentiometer. Just problem that when I run power leds, I get 8.4 V instead of 11.34V. So this is reduce the max. light intensity. If I run power leds without LM350 system, I get 10 V and it is enough for me. You will see my circle at below. I need your helps.
Thanks..
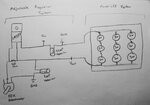