mr_byte31
Full Member level 5

Hi All,
I would like to control washing machine AC motor to have speed of 80 RPM. I know it sounds weird but this is just a part of the project.
I was thinking to use the same concept of DC motors to control the speed of AC motors. the easiest thing was to use PWM technique.
I would use 220V source and the circuit should look like this :
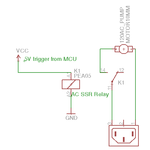
I would use 220 V source and LM555 to be the trigger of the Relay.
would that work ?
I would like to control washing machine AC motor to have speed of 80 RPM. I know it sounds weird but this is just a part of the project.
I was thinking to use the same concept of DC motors to control the speed of AC motors. the easiest thing was to use PWM technique.
I would use 220V source and the circuit should look like this :
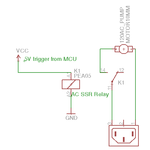
I would use 220 V source and LM555 to be the trigger of the Relay.
would that work ?
Last edited by a moderator: