Sajjadkhan
Full Member level 5

- Joined
- Sep 25, 2010
- Messages
- 307
- Helped
- 17
- Reputation
- 34
- Reaction score
- 16
- Trophy points
- 1,298
- Location
- Rawalpindi,Pakistan
- Activity points
- 4,199
I have two questions about this device which are not mentioned in the data sheet. I have plenty of them so I have to use them.
1. Can I use these devices in parallel (as I have seen people used in inverters). But have a look at my config.
2. The graph of Vds Vs Id curve shows the relation with respect to pulsed voltage. In my case it will be a pure DC current and voltage. 30V of source and load will be of 10V min and 50 Amps current. So voltage across drain-source will be 20V at worst. If the config is possible then how much mosfets do I need I parallel?
Ambient temperature =40 – 42 degree C.
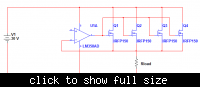
1. Can I use these devices in parallel (as I have seen people used in inverters). But have a look at my config.
2. The graph of Vds Vs Id curve shows the relation with respect to pulsed voltage. In my case it will be a pure DC current and voltage. 30V of source and load will be of 10V min and 50 Amps current. So voltage across drain-source will be 20V at worst. If the config is possible then how much mosfets do I need I parallel?
Ambient temperature =40 – 42 degree C.
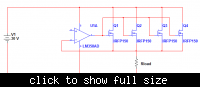