Introduction:
For round pins with precision critical diameters, multiple barrel diameter variations, and drilled holes, CNC machining is the ticket. For the other one-billion-part application
s, metal forming, and fabrication processes offer the best solutions.
Consider the following examples:
1. A formed post with a threaded hole for screw-down wire attachment.
2. A razor-sharp V-stamping for attaching wires by insulator displacement.
3. Lightweight swaged tubular pins attached end to end on a reel for high-speed PCB assembly.
4. Eye-of-needle stamped pins on bandolier for a high-speed PCB assembly
5. Cantilever beam stampings on bandolier for selective gold plating.
6. Ultra-thin stamped leads that can fit on 0,5mm pitch or less.
7.Durable and bend forgiving, phosphor bronze 0,635mm square post extruded wire
8.Drawn wire under 0,0762mm in diameter for medical surgery.
9. Stamped and punched conductive metal frames with multiple holes, slots, and cut-outs.
10. Rolled wire, drawn to target diameter and tensile, straightened and cut to length.
11. A complex multiple feature stamping made in a progressive die.
12. A long deep through-hole typically found in a hypodermic needle
13. An extruded hexagonal tube.
Material forming and fabrication processes such as rolling, stamping, drawing, and extruding allow product designers to create flat and tubular part geometries. These processes are cost-effective and generate minimal scrap. Typically, these technologies are utilized in high-volume
commercial products since their cost per piece is the lowest.
What determines which process is the best?
Each manufacturing process has its characteristic strengths and weaknesses. The weakness of one process is the strength of another. Attempting to emulate the capabilities and strengths of another manufacturing process is neither efficient nor cost-effective. And it will backfire over time, as awareness to the correct process will surface.
There is an inverse relationship between machining and forming alloys, the better the machinability of an alloy the worse the forming capability and vice versa.
Metal forming and fabrication are used everywhere and opens the doors to design interconnects that are not possible by turning. Examples are:
Wire Coiling to create:
a. Compression spring coils.
Cold-Forming to create:
a. Flat bottom holes, since there is no drill point.
b. Compliant barrel cold-formed socket receptacles.
c. Rivets and eyelets.
Drawing to create:
a. Long shells with deep holes such as found in a stainless-steel needle.
b. Straight wire at target tensile strength.
c. Coiled wire for structural and electrical applications.
Extruding / Cut-Wire to create:
a. shells with rectangular, hexagonal, or other polygon-shaped holes.
b. Long round or polygon-shaped tubes.
c Durable and bend resistant 0,635mm square post pins
Stamping/ Punching to create:
a. Flat stamped conductive frames.
b. Pins on a bandolier for selective plating and auto-insertion.
c. Fine pitch 0,5mm or less flat stamped pin leads.
d. Cantilever beam leaf springs.
e. Flat frames with cut-outs, holes, and slots.
f. Sharp 90-degree flat frames and structures.
Swaging to create:
a. Lightweight, hollow tubular round pins.
b. Hollow tubular pins end-to-end on a reel.
c. Solid round and square pins end-to-end on a reel.
Cold-forming, stamping, and cut-wire technologies can manufacture mechanical hardware, electrical
Every manufacturing technology has its associated tooling, process, programming, and setup costs.
The challenge is to select the best manufacturing process suited to the application.
Formed and stamped technologies can create part geometries not possible through precision turning.
They can use lead-free and high-conductivity alloys like copper, as well as high-strength corrosion-resistant alloys like stainless steel. Corrosion-resistant alloys that do not require plating.
Summary:
Metal forming and fabrication offer solutions to the product geometry challenges that turning was not intended. Depending on the alloy used, formed, and extruded products can perform as mechanical structures, electrical conductors, or a hybrid of both. The machinability index of an alloy is a good indicator if the product should be approached using forming or turning manufacturing methods. Depending on their intended function, formed products can utilize lead-free (copper) and corrosion-resistant (stainless steel) alloys. Although a stamping method requires an initial investment of a stamping die design, the vast cost advantages are realized when manufacturing at major production volumes. Metal forming produces minimal material waste compared to machining.
PDF : https://drive.google.com/file/d/1YzCd2UXxMpxeQJMqGYl35kx60UWzm6W6/view?usp=sharing
For round pins with precision critical diameters, multiple barrel diameter variations, and drilled holes, CNC machining is the ticket. For the other one-billion-part application
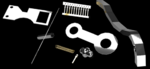
Consider the following examples:
1. A formed post with a threaded hole for screw-down wire attachment.
2. A razor-sharp V-stamping for attaching wires by insulator displacement.
3. Lightweight swaged tubular pins attached end to end on a reel for high-speed PCB assembly.
4. Eye-of-needle stamped pins on bandolier for a high-speed PCB assembly
5. Cantilever beam stampings on bandolier for selective gold plating.
6. Ultra-thin stamped leads that can fit on 0,5mm pitch or less.
7.Durable and bend forgiving, phosphor bronze 0,635mm square post extruded wire
8.Drawn wire under 0,0762mm in diameter for medical surgery.
9. Stamped and punched conductive metal frames with multiple holes, slots, and cut-outs.
10. Rolled wire, drawn to target diameter and tensile, straightened and cut to length.
11. A complex multiple feature stamping made in a progressive die.
12. A long deep through-hole typically found in a hypodermic needle
13. An extruded hexagonal tube.
Material forming and fabrication processes such as rolling, stamping, drawing, and extruding allow product designers to create flat and tubular part geometries. These processes are cost-effective and generate minimal scrap. Typically, these technologies are utilized in high-volume
commercial products since their cost per piece is the lowest.
What determines which process is the best?
Each manufacturing process has its characteristic strengths and weaknesses. The weakness of one process is the strength of another. Attempting to emulate the capabilities and strengths of another manufacturing process is neither efficient nor cost-effective. And it will backfire over time, as awareness to the correct process will surface.
There is an inverse relationship between machining and forming alloys, the better the machinability of an alloy the worse the forming capability and vice versa.
Metal forming and fabrication are used everywhere and opens the doors to design interconnects that are not possible by turning. Examples are:
Wire Coiling to create:
a. Compression spring coils.
Cold-Forming to create:
a. Flat bottom holes, since there is no drill point.
b. Compliant barrel cold-formed socket receptacles.
c. Rivets and eyelets.
Drawing to create:
a. Long shells with deep holes such as found in a stainless-steel needle.
b. Straight wire at target tensile strength.
c. Coiled wire for structural and electrical applications.
Extruding / Cut-Wire to create:
a. shells with rectangular, hexagonal, or other polygon-shaped holes.
b. Long round or polygon-shaped tubes.
c Durable and bend resistant 0,635mm square post pins
Stamping/ Punching to create:
a. Flat stamped conductive frames.
b. Pins on a bandolier for selective plating and auto-insertion.
c. Fine pitch 0,5mm or less flat stamped pin leads.
d. Cantilever beam leaf springs.
e. Flat frames with cut-outs, holes, and slots.
f. Sharp 90-degree flat frames and structures.
Swaging to create:
a. Lightweight, hollow tubular round pins.
b. Hollow tubular pins end-to-end on a reel.
c. Solid round and square pins end-to-end on a reel.
Cold-forming, stamping, and cut-wire technologies can manufacture mechanical hardware, electrical
Every manufacturing technology has its associated tooling, process, programming, and setup costs.
The challenge is to select the best manufacturing process suited to the application.
Formed and stamped technologies can create part geometries not possible through precision turning.
They can use lead-free and high-conductivity alloys like copper, as well as high-strength corrosion-resistant alloys like stainless steel. Corrosion-resistant alloys that do not require plating.
Summary:
Metal forming and fabrication offer solutions to the product geometry challenges that turning was not intended. Depending on the alloy used, formed, and extruded products can perform as mechanical structures, electrical conductors, or a hybrid of both. The machinability index of an alloy is a good indicator if the product should be approached using forming or turning manufacturing methods. Depending on their intended function, formed products can utilize lead-free (copper) and corrosion-resistant (stainless steel) alloys. Although a stamping method requires an initial investment of a stamping die design, the vast cost advantages are realized when manufacturing at major production volumes. Metal forming produces minimal material waste compared to machining.
PDF : https://drive.google.com/file/d/1YzCd2UXxMpxeQJMqGYl35kx60UWzm6W6/view?usp=sharing