ehabzaky
Junior Member level 3

- Joined
- Jun 18, 2015
- Messages
- 25
- Helped
- 0
- Reputation
- 0
- Reaction score
- 0
- Trophy points
- 1
- Activity points
- 269
Dear All,
I'm creating a PCB for a digital switch circuit using Triac as a solid state relay. The circuit is attached below:
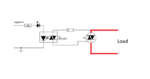
The circuit is using BTA24-600B Triac and MOC3021 Optocoupler. The circuit will drive high loads as the Triac can drive up to 24 Amp current. I'm on the PCB design phase I need some expert person to help me on the following please:
1- I have used online Trace calculators to know the suitable trace width that can carry 24 amperes. I need to know does this current will pass only through the Triac Terminals 1 and 2 to the load? i.e. the red wires in the above drawing only? Should any other black wire carry high current other than the red ones? I have read the datasheet for the Triac but couldn't understand this info.
2- Is there any distance requirement between high current traces on PCB? I have seen trace width calculators but do not know is there any minimum trace spacing requirement?
Any support will be highly appreciated.
Regards,
Ehab Zaky
I'm creating a PCB for a digital switch circuit using Triac as a solid state relay. The circuit is attached below:
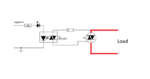
The circuit is using BTA24-600B Triac and MOC3021 Optocoupler. The circuit will drive high loads as the Triac can drive up to 24 Amp current. I'm on the PCB design phase I need some expert person to help me on the following please:
1- I have used online Trace calculators to know the suitable trace width that can carry 24 amperes. I need to know does this current will pass only through the Triac Terminals 1 and 2 to the load? i.e. the red wires in the above drawing only? Should any other black wire carry high current other than the red ones? I have read the datasheet for the Triac but couldn't understand this info.
2- Is there any distance requirement between high current traces on PCB? I have seen trace width calculators but do not know is there any minimum trace spacing requirement?
Any support will be highly appreciated.
Regards,
Ehab Zaky